A race against time for design and production
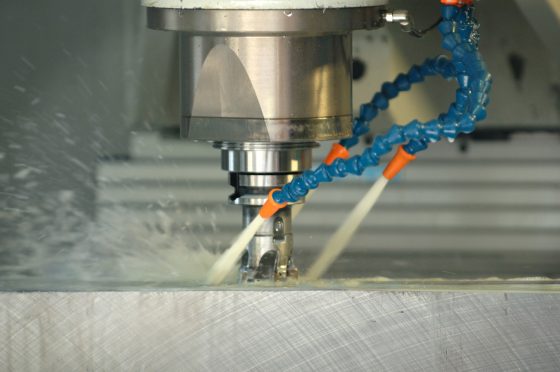
For many of our customers their products are constantly going through re-design and development for improvement; we have to align ourselves with that process, often against tough deadlines.
The challenge:
To replicate a moulded rubber HNBR component in FKM (Viton®), which has a very different shrinkage rate and therefore required a new tool. The customer needed the component for the next race, and with the added time required for testing this meant an extremely tight deadline.
The outcome:
The FKM moulded rubber components passed dyno testing as predicted, were raced successfully, and continued as the preferred part for the rest of the season.
Anyone who has watched Formula 1 knows that everything is fast. Extremely fast. The same is true behind the scenes, off the track; marginal gains are sought between each race, problems must be addressed – re-designed, prototyped, tested, proven, manufactured and delivered – before the next race, usually in a different part of the world.
It’s an exhilarating industry to be involved in, but it also demands extremely responsive, innovative thinking and the ability to respond very quickly. As a supplier, if you can’t fulfil that brief, you may as well step aside.
When this customer came to us in the autumn looking for improvement, collaboration with their engineers began immediately. An HNBR engine part that we had been supplying for a while had become overstressed by a revised engine characteristic, and was becoming a reliability concern, so we recommended FKM (Viton®) as a good alternative given the engine change. The two materials have shrinkage rates different enough that a new tool would have to be manufactured in order to produce a finished part within tolerance in the new material.
A secondary challenge was that the original HNBR part would remain in circulation for the time being, and because a change in colour would reduce the tear strength (carbon black gives rubber its strength, and a bi-product of carbon black is the colour), we needed to find a solution to part-marking. A number engraved into the tool (and therefore raised on the part), would have impacted the function of the part, and so the solution we used was laser etching post manufacture.
We fast-tracked the manufacture of the new tool and undertook rapid manufacture of parts so that the customer could undertake testing and approve parts for final production all before the next race. The final production parts were delivered the day that they were manufactured in time for the next race.