Custom solutions to ensure MXGP pole position
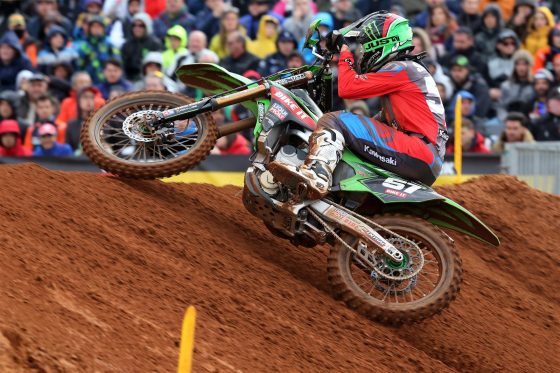
Not all our customers want volumes of parts; sometimes they just need a small batch, manufactured to exacting specifications with absolute performance in mind.
Challenge:
To design and produce parts for improved performance on a competition racing engine for a Kawasaki 250f.
Outcome:
The engine delivered class-leading performance and race wins in the MX GP.
Steve Dixon is a household name in the world of motocross. He has lead countless riders to British championships and to victories in MXGP, and for many years now has been teamed up with Bike It to produce class-leading bikes and riders.
Working with Steve Dixon’s Bike It DRT Kawasaki racing team on Cosworth’s DRT KX250 for the MX2 World Championship, we were asked to develop modified engine components to upgrade a standard competition engine. The racing team had already designed custom engine parts in collaboration with Cosworth, and our challenge was to develop solutions in three areas to accommodate their modifications:
- Cam chain guides for a modified configuration of cam chain
- A non-standard manifold to optimise the inlet tract on the fuel injection system
- A special seal for a non-standard airbox
Because of the way that a team like this works – one-offs, custom builds – there was no CAD data. We were provided with sketches and sectioned standard engine components from which we measured and then modelled proposed parts. We had standard components available, which we used to analyse the material specifications to ensure like-for-like or improved performance in terms of materials – particularly in providing solutions that offered reduced friction and increased resilience.
We developed several proposals for each component, modelled them using CAD, and then CNC machined them using engineering plastics in order that each of the designs could be sampled for fit and function by the team. Cosworth took the decision about which version of the designs to opt for, and we made production tooling and subsequently produced the rubber mouldings and bonded parts for delivery to an extremely tight deadline for tests.
The customer was extremely pleased, and Steve Dixon said this of our service:
“We need our suppliers to be versatile, innovative and responsive. As always, Martin’s delivered all three of those elements on this project and helped in getting us to pole position again.”
Download a copy of this case study here.