High temperature grades of rubber
Posted on 12/06/2023 Category: Rubber moulding, Rubber Testing, Technical Features
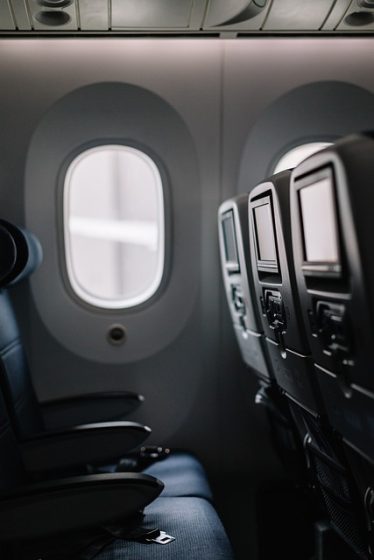
The increasing demands of new technologies, particularly those being developed for aerospace, UAVs, electric vehicles and in the energy sector, mean a greater need for seals and other rubber components be made from materials which are resistant to high temperatures.
What do we mean by ‘high temperature resistant’?
The first thing to clarify is that high temperature resistance in rubber is not the same as fire retardancy; the requirements are very different and therefore the additives used in the compounds are also different. Fire retardancy in rubber means that the material will not release noxious chemicals when alight, and is designed primarily for the health and safety of those in the vicinity of a fire. High temperature resistant rubber are those which will not deform or degrade when exposed to temperatures in which standard rubbers may not maintain structural integrity.
How high is ‘high’ when we talk about temperature resistance in rubbers?
As with all things, the term ‘high’ is relative and will depend on the type of elastomer and application in question; high temperatures for elastomers can be considered to be anything over ambient or room temperature – for natural rubber, a high temperature could be +70°C, whereas for fluorinated rubber high temperature could be 230°C. High operating temperatures for elastomers are often low in comparison to other materials. Above temperatures of 175°C, the only available options for elastomers are silicone, which will manage temperatures in excess of 200°C, and fluorinated elastomers, which can withstand temperatures of up to 315°C.
All elastomers have an operating temperature range and each has a blend of properties and performance, and the balance that you opt for when selecting a rubber material will depend on the application in question and the priorities in terms of operating conditions.
What enables high temperature resistant rubbers to perform outside of standard elastomer operating temperatures?
The upper temperature limit of organic elastomers – those with a carbon backbone – is determined by the bond strengths of the constituents in the polymer and the curing mechanism used. Specialist grades of elastomer, such as fluorinated polymers (FKM), can resist temperatures over 200°C.
Fully fluorinated elastomers, known as perfluoroelastomers (FFKM), when compounded and cured correctly, can withstand temperatures up to 316°C. The reason for the specific temperature ceiling is that beyond this, the elastomer begins a de-fluorination process and will eventually thermally decompose; the material may be able to cope with short periods above this threshold but in turn its service life will be significantly reduced.
Inorganic elastomers such as silicone have a temperature stable siloxane backbone that can resist temperatures in excess of 200°C, and the thermal degradation process can be stabilised further still to achieve resistance to temperatures up to 300°C.
Each elastomer material will have an upper temperature limit, and by use of specific curing mechanisms or compounding ingredients such as stabilisers, the upper limit may be slightly extended or the performance at elevated temperature can be improved.
Implications of opting for temperature resistance in rubber
The application of a rubber component is critical in specifying a suitable material. Silicone is often the go-to high temperature rubber but it must have oxygen present in order to sustain its structure – and the higher the operating temperature, the more important this is. Thermal degradation softens the rubber, whilst oxygenation increases the hardness, and silicone rubber requires a careful balance between these two processes to maintain its properties for extended periods at elevated temperatures. If you exposed a silicone component to 200°C in the absence of oxygen, you would find yourself with a puddle, which is why you won’t find silicone used in an environment where saturated steam is present.
Similarly, the curing systems used in FFKM have an impact on the temperature range that the material will withstand, but the application is what drives that decision on curing system. The curing system in a rubber compound enables crosslinks to be created during the vulcanisation process, but because they are chemical additives, they don’t necessarily respond well to some environments. For example, a peroxide curing system in FFKM is good for applications where water and steam are present, but will only withstand 230°C. A bisphenol cure system will provide a working temperature of 280°C but is poor in acids. Triazine, the most effective in terms of temperature resistance – offering up to 316°C – is very poor in water and steam.
The intended application for any rubber component is crucial when looking at which compound to use for the temperature range in question. When elastomers are subject to compression (for example, a seal under load), the objective is for that component to return to its original cross section when the load is removed. This is known as compression set, and this is the property of rubber which is most affected by temperature. Therefore, when considering a rubber for a sealing application at high temperatures, careful consideration needs to be given to material selection.
In terms of monetary cost, high temperature resistant elastomers such as silicone rubber and FFKM may cost more than other elastomers due to the specialist nature of the compound and the more complicated polymerisation process. To add to a material’s low temperature flexibility in addition to its high temperature resistance can significantly increase the material cost even further.
How to select the right elastomer for your high temperature application
The process of selecting a suitable material, as outlined above, is not as simple as looking at the service temperature that your product will experience. Alongside this, the environment and application are also critical, alongside the curative selection and the consistency of temperature during the product’s service life.
Our team includes technical specialists with experience in material selection as well as finite element analysis tools to fully understand how a component will perform within a particular application when moulded from a specific rubber compound. If you are developing a product that will be required to perform in extreme environments, including high temperatures, it is always better to seek advice from the outset to ensure that the compound and component design will behave as you intend.
Contact us to chat to one of our expert about your high temperature application.