Designing for production efficiencies
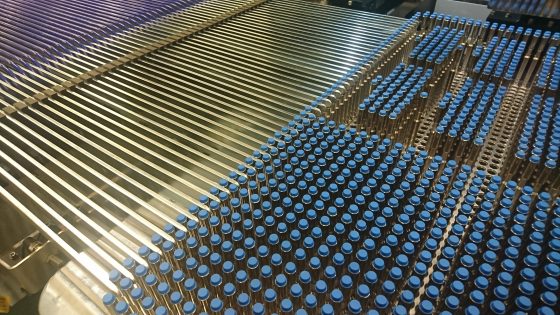
The processing industry is under pressure to offer efficiencies and cost-savings at all stages of their process. Consistent, reliable supply is the backbone of a productive business – and sometimes design for manufacture is key.
The challenge:
To offer a service to supply in a short timescale a variety of products for an unpredictable order forecast; the customer required a guaranteed delivery to a schedule to fulfill production requirements. With no CAD data to work with, reverse engineering was needed to replicate the part.
The outcome:
We are now supplying a functional part to schedule and within the necessary cost bracket.
Blankmaster manufactures and supplies converting equipment to the print and packaging industries. Their customers are manufacturers of folding cartons, blister cards, plastic in-mould labels and greetings cards, to name just a few.
Blankmaster came to us looking for components for their Kawahara TXR-1100, a blanking machine that automates the process often carried out by hand stripping – i.e. removing the surplus material from a die cut sheet, in bulk.
We proposed a larger 100 cavity tool, with colour-coded hardnesses for ease of identification. In terms of the production solution, in order to minimalise tooling costs we made allowances for the differing shore hardnesses, ensuring that we could produce all the options from the same tool but within tolerance. We opted for a transfer mould tool to deliver parts with high accuracy but minimal finishing requirement, with parts cryogenically de-flashed for speed.
We are now supplying production volumes and the customer is very pleased with the outcome. Gary Compton, Managing Director of Blankmaster, has said of the design and manufacture process:
“As a manufacturer we are well aware of the importance of designing for consistency, quality and repeatability. We are extremely happy with both the product and the service that we have received from everyone at Martin’s – we are now able to deliver our own product with confidence.”