Rubber manufacturing words
and terminology
Over the last 150 years or so, the rubber industry has developed many words and terms that are unique to it, and our Rubber Glossary is intended to help clarify what is meant by these words.
The longevity of the industry means that some terms are rarely used these days, or have become associated with the more recent development of thermoplastic materials rather than the traditional thermoset rubbers that were discovered in the 1840’s, giving rise to the industry we have today. In our “A-Z “rubber glossary we have covered this crossover of materials, as well as looking at terms commonly used in the applications where rubber is a key constituent, such as sealing and hydraulics.
If the term you are seeking does not appear in this rubber glossary list, please contact our Technical Team, who will be pleased to help you.
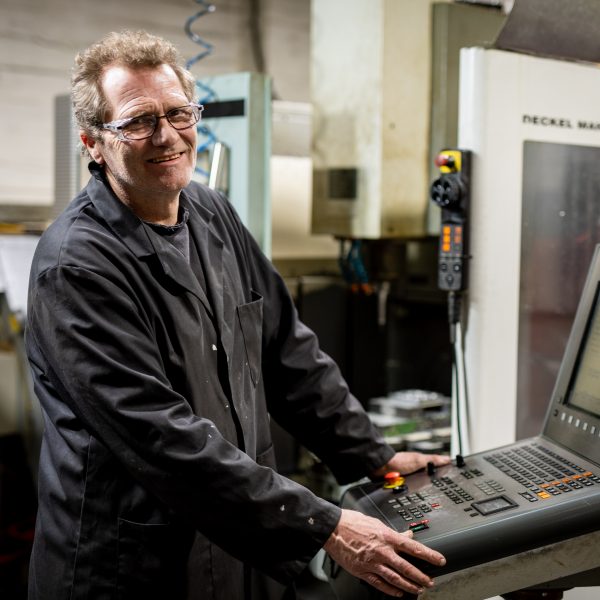
Tapping natural rubber from tree plantations, see our A-Z Rubber Glossary for an explanation of Hevea Brasiliensis
“A” Face
The cosmetically important areas or faces of a component, typically such as cabin trims or interior components that are in public view when in service.
Abrasion
The process of wearing down or rubbing away by means of friction.
Abrasion Resistance
The ability of a rubber compound to withstand mechanical deterioration due to mechanical wear such as rubbing, scraping or erosion, that tends to remove material from its surface. Abrasion properties of rubber are difficult to define. Many different abrasion machines have been designed but they do not always give similar results. The most common abraders are AKRON, Dunlop and DuPont. Results are recorded as volume loss per standard test piece, or as the difference in volume loss when compared with a standard material of known abrasion value. Indices of relative abrasion are also used.
ABS
Acrylonitrile-butadiene-styrene.
Absorption
The physical attraction and incorporation of a substance (liquid, gas, or vapour) into a material’s interior.
Accelerated Ageing
Heat ageing is widely used as a method of evaluating long term ageing properties. Hardness and dumbbell type tensile test pieces are placed in an air circulating oven for a specific period of time at a given temperature (e.g. 7 days at 70°C). The properties of the rubber are then tested and compared with the properties before ageing. The percentage retained for each property is recorded.
Accelerated Life Test
Test conditions designed to reproduce, in a shortened time period, the deterioration a product will obtain in its normal conditions.
Accelerated Service Test
Exaggeration of service conditions such as speed, temperature, or continuity of operation, for the purpose of testing and evaluation of a material in a shorter amount of time.
Accelerators
Chemicals which are added to natural or synthetic rubbers to accelerate the rate of vulcanisation. Rubber without accelerators takes twenty or thirty times longer to cure.
Acetal
Also known as POM or Delrin®, this tough engineering plastic features high abrasion and heat resistance, low friction and water absorption (unlike Nylon) and good electrical insulation along with good dimensional stability.
Acid acceptors
Mostly used in Chloroprenes (Neoprene) to absorb the acid produced by the chemical reactions taking place during curing. Acid acceptors are usually metal oxides.
Acid Resistant
A material that can function in an acidic environment.
Activators
Chemicals which are added to rubbers to activate curing.
Actual Size
The precise size of an o-ring or seal in decimal dimensions, inches or millimetres, including tolerances and energisation allowances. See also “Housing Size”
Adhere
Clinging or sticking of two surfaces.
Adhering Flash
Extremely thin flash (usually less than .002′ thick) that adheres to the finished part during moulding or deflashing processes.
Adhesion
The tendency of a material to cling to a contact surface.
Adhesives
The family of substances used to adhere by various methods two parts together. For rubber materials, Contact, Epoxy, Cyanoacrylate, RTV or hot vulcanising adhesives are all suitable options depending on the application.
Aflas®
A recent synthetic rubber with exceptional high temperature performance, surviving 230°c continuous service, with superior chemical, oil and fuel resistance, and unlike fluoroelastomer, good steam resistance. Often used in Oil & Gas applications where extreme performance is required, but, an expensive option.
Age Protection – Active
The use of a chemical additive in a rubber compound which is preferentially attacked by oxygen or ozone thereby sacrificially protecting the rubber. See also “Anti-Ozonant”.
Age Protection – Passive
The use of a chemical additive in a rubber that will migrate to the surface of a rubber part to form a protective physical barrier.
Aging
The process of, or the results of, exposure of rubber to natural or artificial environmental conditions for a prolonged period of time, resulting in changed physical properties or appearance.
Air Checks
Surface markings resulting from the trapping of air between the material being cured and the mould surface. See also “Laking”
Air Curing
Using hot air ovens or steam to vulcanise rubber.
Alloy
A composite material produced by blending polymers or copolymers with other polymers under selected conditions to achieve greater physical properties.
Backrinding
A “breaking up” of the rubber normally observed as a ragged indentation around tool split lines. It results from the rubber shrinking during cure and tearing away at points where the moulding is held.
Backup ring
A washer-like device of a relatively hard, tough material installed in the gland on the downstream side of the seal to prevent seal extrusion into the diametrical gland gap between rod and housing while under pressure. Typically used with O rings and U Seal designs. Sometimes called a Back-Up Washer.
Banbury Mixer
An internal mixer commonly used in the rubber industry. It consists of two shaped rotors which turn inside a sealed chamber, to masticate the rubber compound and fully mix all the various constituents.
Barrel
That part of an extruder inside which the feed screw is located.
Base Line
The mark or datum from which all features are dimensioned.
Batch Control
A process of keeping separate a batch of a rubber compound from the time it is moulded through the entire production process up to and including the Shipping Department.
Batch Number
The unique assigned number that identifies a particular batch of rubber compound or finished parts made in any given production run, in aid of traceability.
Blank
Term used for weighed up material stock that is placed in the mould for making a cured part. See also Preload.
Blast Finishing
The process of removing flash from moulded objects and/or dulling their surfaces, by impinging media such as crushed apricot pits, walnut shells or plastic pellets upon them with sufficient force to fracture the flash.
Bleeding
The exudation or migration of droplets of excess plasticiser or other compound elements onto the surface of a rubber product. This happens when rubbers contain unsuitable levels of plasticisers which are not fully compatible. See also Blooming.
Blemish
Anything impairing the appearance of a compound, such as a mark, deformity, or injury.
Blister
An imperfection on the surface of a rubber article caused by a pocket of air or gas beneath the surface.
Bloom
A milky surface discoloration caused by the migration of certain compound components (such as antiozonants, lubricants, stabiliser pigment, plasticisers,) to the rubber’s surface after moulding or storage. The waxy or crystalline film can be deliberate and designed to serve as a protective coating shielding the part from oxidation. This discoloration DOES NOT adversely affect material performance.
Blow Moulding
A moulding process usually for thermoplastic or glass materials, whereby a tube of heated material is held vertical and clamped at the lower end in a mould, then inflated to “blow” out against the mould surface and create the required geometry. Once cooled the part can be extracted from the mould.
Bond
The mechanical or chemical force that holds an elastomer to some other object. Mechanical bonding includes component interference or a physical fixing and no molecular cross-bridging between the elastomer and substrate, whereas chemical bonding involves contact or epoxy cold bond adhesives, or full vulcanisation with heat and pressure to adhere an elastomer to a primed surface.
Bore
A hole machined in a component, which permits the passage of a shaft.
Break-out Friction
The frictional force developed at start-up, due to the tendency of seals or O rings to adhere to the micro fine grooves of surrounding surfaces.
Brittleness
Tendency to crack upon physical deformation.
Brittleness Temperature
The temperature at which plastics and elastomers rupture by impact under specified conditions.
BS
British Standard, controlled and issued by BSI, now usually in line with an equivalent ISO Standard.
BSI
British Standards Institution, UK model for quality assurance in design, development, production, installation and servicing.
Building Tack
Term used to describe the ability of a rubber to stick to itself in the uncured state, so allowing pre-building of the material before curing.
Bumping
The action of cracking and re-closing a press during the first stage of the cure cycle to release gas and move rubber around further inside the mould cavity.
Bun
The large slab of sponge rubber which is produced as the bulk moulded blank, from which various thicknesses of sheet required are then skived off to create the semi finished materials for final conversion into finished strip and gaskets. The outer surface of the Bun is skinned, and only sheets with this outer surface will therefore have a skin, usually only on one side.
Buna N
A general term for the copolymer butadiene and acrylonitrile also referred to as NBR or Nitrile.
Buna S
The copolymer of butadiene and acrylonitrile also referred to as SBR.
Burned
Showing evidence of excessive heating during processing or use of a rubber, as evidenced by blistering, discolouration, distortion or destruction of the surface.
Butyl
A copolymer of isobutylene and isoprene. Bromobutyl.
Butyl
An early synthetic rubber which exhibits particularly good weathering and gas permeability performance, and as such is used extensively for gas tight seal. It has reasonable physical properties although it does not resist oils and fuels well. It finds wide application in tyre inner tubes, NBC protection and roofing or pond lining materials.
Calendar
The process and machine required for turning uncured rubber into sheets or lengths by squeezing it in a multi-rollered machine to form thin sheets of uncured compound. When the rollers are heated, also used to produce cured sheeting for onward processing. Also used to coat or impregnate fabric with rubber compound.
Carbon Black
A black material used as a filler in rubber. It gives the rubber its black colour and the hardness characteristics, and adds to the physical strength of the material.
Cavity
A depression, or a set of matching depressions in a mould tool which forms the outer surfaces of the moulded articles. These features are directly responsible for forming the final shape of a moulded part, and the detail on them is directly transferred to the part produced from the cavity.
Charge
The measurement or weight of material used to load a mould during one cycle. Also see “Shot Weight”
Chemical bonding
A method for bonding rubber to secondary parts by applying special adhesives or primers to the substrate prior to moulding.
Chemical Resistance
This is usually expressed as the change in properties (such as hardness, strength and elongation at break) caused by the presence of chemicals under defined conditions (including concentration, time and temperature).
Circularity
The form tolerance of the surface of a moulded or ground ball in reference to a perfect sphere. Also referred to as “roundness”
Clamping Pressure
The pressure applied to the mould to keep it closed during a cycle. In injection moulding and in transfer moulding; the pressure which is applied to the mould to keep it closed, in opposition to the injection or fluid pressure of the moulding material.
Clay
Commonly used as an “extender” in rubber. Treated clays reinforce the rubber and are termed “hard” clays. Those which do not provide reinforcement are called “soft” clays.
Clearance, diametrical
The gap, formed by the mating metal surfaces, which a seal has to close to prevent leakage in the system.
Clearance (in a sealing system)
The space between components in a mechanical system which is present to allow for manufacturing, thermal, and dynamic variations in the size and position of the components. As measured, it is equal to the distance between the sealing surface and the entrance to the seal groove. In a radial sealing system, this will be the space between the O.D. of the shaft or piston and the I.D. of the bore. As the clearance in a system increases, the tendency of the seal to dislodge from the groove and enter into the clearance space also increases, especially in applications where pressure is present. Anti-extrusion measures should be considered in these cases. Care should be taken in radial applications to note whether clearances are being stated as radial clearances or as diametrical clearances.
Cloth Finish
Rubber sheeting that has a textured finish imparted by running a layer of fabric through the calendar during the curing process. Certain gasket designs work better with a cloth finish to the material.
Co extrusion
The process of extruding two or more materials through a single die with two or more orifices arranged so that the extrudates merge and weld together into a laminar structure before chilling to form the finished product.
Coating
A uniform layer of chemical primers or adhesives applied to a surface to produce a chemical bond between the rubber and substrate. May also refer to special surface treatments that can be applied to rubber to achieve desired properties such as ozone protection.
Coefficient of Friction
Ratio of the force needed to move an elastomer over a given surface to the total forces pressing on the elastomer and surface.
Coefficient of thermal expansion
Average material expansion per degree of temperature over a defined range, expressed as a fraction of the initial dimension.
Cold flexibility
The flexibility still remaining in an elastomer after exposure to low temperature for a specific amount of time.
Cold Flow
A term describing the tendency of certain materials to continue to deform or “creep” under constant sealing pressure (compressive load)
Cold Resistant
The ability of a seal to function at low temperatures, influenced by both design and material.
Composite
An article or substance containing or made up of two or more different substances.
Compound
An unvulcanised mixture of a polymer and associated chemical ingredients necessary to produce a finished rubber like material. The term is commonly used when referring to a specific rubber formulation or recipe.
Compounding
The step of mixing base polymer with additives such as stabilisers, fillers, pigments into a form suitable for processing into finished articles.
Compression modulus
The stress to strain ratio of a tested material, expressed as a fraction of the original height or thickness in the direction of the applied force.
Compression Moulding
A method of moulding in which the moulding material, sometimes preheated, is placed in an open heated mould cavity, the mould is closed with a top force, pressure is applied to force the material into contact with all mould surfaces, both heat and pressure are maintained until the moulding material has cured. This process is most often used with thermoset materials.
Compression Set
The degree to which a rubber does not recover fully to its original state after it has been compressed for a long period of time. The term is commonly used in reference to a test conducted under specific conditions wherein the permanent deformation, expressed as a percentage, is measured after a prescribed period of time. A low compression set is desirable in moulded rubber parts such as seals and gaskets, which must retain their dimensions to maintain an effective seal.
Compression Set Test
A cylindrical button of rubber of known thickness is compressed to a fixed height (typically 70% or 75% of its original height) at a defined temperature for a specific period of time. The button is then released, allowed to recover (typically for 30 minutes) and the thickness is measured. Compression Set is the height that is not recovered expressed as a percentage of the amount by which it was compressed.
Compressive Strength
The load sustained by a test specimen in a compressive test divided by the original area of the specimen.
Concentricity
A condition in which two or more features (cylinder, cones, spheres, hexagons, etc…) in any combination, have a common axis.
Conditioning
Subjecting a material to standard environmental and/or stress history prior to testing.
Contact Adhesive
An adhesive consisting of a material suspended in a solvent carrier, which, once applied to a substrate and the solvent having been allowed to evolve, leaves a tacky layer of adhesive material which, when mated with a similar layer of adhesive, forms a bond on contact. Many types of solvent and adhesive systems exist, but all rely on accurate placement of the mating parts first time.
Conversion Celsius to Fahrenheit
C = (° F – 32) x 5.9 F = (° C x 9.5) + 32
Conversion Fahrenheit to Celsius
F= (° C x 9/5) +32 C= (° F – 32) x 5/9
Conversion Kilograms to Pounds
kg = lbs x 0.454 lbs = kg x 2.205
Conversion Millimetres to Inches
mm = in x 25.4 in = mm x 0.03937
Conversion Pounds to Kilograms
lbs = kg x 2.205 kg = lbs x 0.454
Cooling Block
Block of metal or wood used to maintain the proper shape or dimensional accuracy of a part after it is removed from the mould until it is cool enough to retain its shape without further appreciable distortion. Also known as “shrink fixture”
Cooling Channels
Channels located within the body of a mould through which a cooling medium is circulated to control the mould surface temperature.
Copolymer
An elastomer (polymer) resulting from the chemical combination of two dissimilar monomers. For example, Buna N from Butadiene and Acrylonitrile.
Copper
When used in thin sections, annealed copper is a useful gasket or shim material, often in high pressure applications.
Cork
This traditional yet exceptionally useful gasket material is a matrix of cork granules held in a rubber binder. The excellent compression set and resilience of cork, coupled with the stability of a rubber binder creates a range of economical but very useful materials. Various grades of cork and rubber are combined to provide a variety of chemical and physical properties suitable for many gasket applications, common trade names being Nebar® and Tico®
Corrosion
Progressive wearing away of a surface because of a chemical reaction.
CPK
Describes how capable the stable process is of meeting design specifications. The CPK measures the distance from the process average (xbar) to the nearest specification and compares it to the natural variation in the process.
Cracking
Sharp breaks or fissures in rubber surfaces resulting from excessive strain or exposure to adverse environmental factors.
Crazing
Fine cracks which may extend in a network on or under the surface or through a layer of rubber or plastic material.
Creep
The continued progressive relaxation of an elastomeric material under constant sealing pressure (compressive load) or stress. Also known as cold flow. Also called shrink.
Cross-linking Agents
A chemical or chemicals that bond the polymer chains of a rubber together during the molding process.
Cross section
The width of a part such as an O-ring or a seal view showing the internal structure at right angles to the mould parting line.
Cross Section-Axial
When the part is flat (relative), the cross section that is at 90 to the linear plane.
Cross Section-Radial
When the part is flat (relative), the cross section in the linear plane.
Cross-Sectional Compression
The deformation placed on a rubber part to affect a seal. It is expressed as a percentage of the seal’s original (undeformed) cross-section. See also Squeeze.
Cross sectional diameter (CS)
One-half the difference between the ID and OD of an O-ring.
Cross-Sectional Reduction (of a seal)
The reduction in thickness of a seal’s cross-section, a result of material displacement caused by an applied stretch to the seal. See also Necking.
Cryogenic Deflashing
Process whereby rubber parts are chilled to low temperatures using liquid nitrogen, and tumbled to break off flash which has become brittle in the low temperature.
Crystallisation
Rubber materials tend to crystallise on standing, resulting in an increase in hardness. This increase is usually small, but can be more significant in the case of some Neoprene (polychloroprene) grades.
CTE
Coefficient of Thermal Expansion: The change in length of a material for a unit change in temperature, per unit of length.
Curatives
The chemicals involved in curing the rubber, e.g. Accelerators, vulcanising agents, activators etc.
Cure
The creation of an elastomer through chemical bonding of polymers and moulded rubber, usually with the help of sulphur and an accelerator, under pressure, at elevated temperatures. See also vulcanisation.
Cure Date
The date that a part was moulded and became fully cured. A product code of 3Q04, for example, indicates a cure date of the third quarter (3Q) of 2004 (04).
Cure Time
The preset time needed to complete the curing process.
Cure Weight
The prescribed weight of stock needed to make one cure of parts, usually stated on the route card, see also Shot Weight and Charge Weight.
Curing
Also known as vulcanisation, this is the permanent change which the rubber undergoes during moulding. When mixed, rubber compounds are thermoplastic and will melt and deform easily. After curing, the rubber is permanently changed by cross-linking into its thermoset vulcanised state. See also vulcanisation.
Curing temperature
The temperature of vulcanisation.
Custom Moulder
A firm specialising in the moulding of items or components to the specifications of another firm which handles the design or distribution of the item, or incorporates the custom moulded components in one of its own products.
Cyanoacrylate
An acrylic resin adhesive developed in the 1940’s which rapidly polymerises when exposed to water, forming very strong bonds across a wide range of rubbers and substrates, although its shear strength is not particularly high. The cured adhesive is rigid and when used to bond rubber to itself can result in a noticeable hard point at the joint.
Cycle Time
In a moulding operation, cycle time is the time elapsing between the start of curing a part and the same point in the next cycle.
Cyclising
The process of acid etching rubber in preparation for bonding with adhesives.
Cylinder
Chamber in which a piston is driven.
Damping
The ability of an elastomer to absorb forced vibrational energy. Different elastomers have different dampening characteristics. For most general applications the lower the material damping is, the better the Isolation; generally, together with its high mechanical properties this is why Natural rubber is the preferred choice for anti-vibration mountings.
Dash Number
A three digit number preceded by a dash as specified by SAE Aerospace Standard 568A to indicate an o-ring size based on inside diameter (I.D) and cross-section (W).
Daylight Opening
The clearance between two platens of a moulding press when in the fully open position.
Deflash
The removal of unwanted, excess material from a finished rubber product.
Deflashing
Any of various processes used to remove extraneous rubber from a moulded rubber part.
Degassing
The removal of unwanted, excess gaseous material from a finished rubber product.
Degradation
A deleterious change in the chemical structure, physical properties or appearance of a rubber or plastic, often caused by exposure to heat, light, oxygen or weathering.
Delamination
Separation of two or more surfaces in a composite material.
Density
(Absolute) Mass per unit volume of a substance, for example expressed in grams per cubic centimetre. See also Specific Gravity.
Diametral Clearance Gap
The difference in diameters between two mating circular surfaces.
Diametrical Clearance
The necessary gap between two mating metal surfaces that move in relation to each other, forming a gland’s internal cavity. Through slight over sizing and accompanying “squeeze” a seal is used to cover this gap and prevent system leakage.
Diaphragm Gate
Used in symmetrical cavity filling to reduce weld-line formation and improve filling rates.
Diaphragm Rubber Sheeting
Premium grade elastomer reinforced fabric sheeting intended primarily for diaphragm applications.
Diaphragm Seals
Precisely produced diaphragms and sensitive flap valves for use in gas controls, valves, actuators, regulators, pumps and metering equipment.
Die
Tooling orifice through which uncured compound is forced in the extrusion process to form a profile.
Die Cut
The process of stamping out the I.D. or O.D. parting line flash or feed from a moulded part. The part is placed on a mechanical fixture to perform this function.
Die Cut Gaskets
Press cut and hand cut gaskets in all types of rubber and non-metallic materials. See also Rule Forme.
Dielectric Strength / Electrical Properties
The resistance of an elastomer to the conducting of an electrical current. Anti-static and conductive properties of rubbers are defined by measuring their electrical resistance. Typical measurements are obtained through the thickness of a sample by using 25mm sq. electrodes under a pressure of 45N and applying a voltage of 500V DC @ approx. 6mA. (Energy dissipated into the test piece is limited to 3W max.) The surfaces should be cleaned before measuring. Patterned surfaces should be wetted with a conductive solution or paint. See also Electrical Safety Matting.
Differential Pressure
The difference in the amount of force being exerted on the high-pressure side of a seal relative to the low pressure side.
Dimensional stability
The ability of a plastic or rubber part to retain the precise shape in which it was moulded.
Dispersion
Finely divided particles of a material in suspension in another substance, typically fillers within rubber compounds need good, even dispersion to deliver consistent material properties.
Double Injection
A moulding defect that is fully avoidable by following proper moulding procedure. It is identified by a flat raised dome that peels away easily. It is caused by not completely unloading a mould of all its products, and running another cure cycle on top of the parts that were left in the mould from the previous cure.
Draft
The degree of taper of a side wall or the angle of clearance designed to facilitate removal of parts from a mould. This is not always necessary on elastomeric mouldings but is required on rigid materials.
Dump Groove
A groove around the periphery of a mould cavity used to an escape reservoir to accept any excess material from the cavity during moulding. Additional material beyond that which is required to fill the cavity is usually introduced into the cavity to ensure that the part is completely formed and to minimize the presence of entrapped air and voids. See also Overflow Groove.
Durometer
Standard rubber industry test instrument, which uses a ball indenter to measure the hardness of an elastomeric material. Shore is one manufacturer and their Shore Hardness scale is well known, but other instruments that measure in the similar International Rubber Hardness Degree scale are also very common.
Dwell
A pause in the application of pressure to a mould, made just before the mould is completely closed, allowing any gases formed or present to escape from the moulding material. See also Bumping.
Dynamic seal
Any seal used in an environment or application involving reciprocating, rotating, or oscillating motion of a shaft or rod relative to its seal. See also Static Seal.
Elastic Limit
Maximum stress that a material will stand before permanent deformation occurs.
Elasticity
A rubber like material’s ability to rapidly return to its original size and shape after removal of any stresses causing deformation such as stretching, compression, or torsion. It is the opposite of plasticity. The term elasticity is often loosely employed to signify the “stretchiness” of a rubber like material.
Elastomer
A natural or synthetic polymer material which at room temperature can be stretched repeatedly and, upon immediate release of the stress, will return with force to its approximate original length. Often, but not necessarily, a material of the rubber family.
Elastomeric
The adjective of Elastomer; describing the general property of a material to behave in an elastic way.
Electric Strength
Describes the ability of a rubber to withstand high voltages. It is usually quoted in KV per mm of rubber thickness. See also Dielectric Strength.
Elongation
Percentage increase in original length of a specimen produced by a tensile force applied to the specimen.
Generally referred to in terms of tensile (pulling apart) testing, elongation is the increase in length of a test specimen, expressed as a percentage of its original (unstretched) length. It is relative to a given load at the breakpoint.
Elongation at Break
Elongation is defined as the length at breaking point expressed as a percentage of its original length at rest. If a rubber sample reaches twice its length before breaking its elongation is 100%.
EMI
Electromagnetic interference.
Encapsulating
Enclosing an article (usually an electronic component) in a closed envelope of plastic or rubber, by overmoulding or potting the object in a casting resin or vulcanised rubber.
Energisation
The method by which a seal will engage with its housing or moving parts. This can be done either by designing an interference fit such that the elasticity of the seal provides a constant force against its housing, or, by ensuring that the application of pressure causes the seal to swell such that an increasingly tighter sealing effect is created. The material of the seal can provide energisation, or it can be assisted by the addition of rubber or spring inserts within the seal design.
Engineering Plastics
A broad term covering all plastics, with or without fillers or reinforcements, which have mechanical, chemical and thermal properties suitable for use in construction, machine components and chemical processing equipment. These materials can be moulded but products are more usually made by machining methods, taking billet stock shapes of the relevant plastic materials and cutting accurate shapes from those billets.
EPDM
A synthetic rubber with very inert chemical properties which gives it great weathering resistance and good all round performance other than contact with fuels and oils. Widely used as a lower cost polymer, with good processing abilities, however the very inert nature of the manterial also means it is difficult to adhere to, and this can be a limitation. Many applications where external weathering will occur, such as construction and architectural glazing installations.
Epichlorhydrin
Another relatively recent synthetic, featuring good oil and weathering resistance, a high temperature limit of 150°c which exceds Nitrile and a low temperature limit of -40°c which also exceeds Nitrile, however it is somewhat weaker than Nitrile and is substantially more expensive.
Epoxy Resin
An adhesive or potting material made of a resin and hardener which when mixed, cure to form a copolymer, often thermosetting to a final state. The mix ratio and various reinforcing additives can give a wide variety of properties, and these systems are particularly useful for bonding rubber to solid substrates.
Evazote®
A crosslinked closed cell ethylene foam that is tougher and more resilient than Plastazote.
Explosive Decompression
When continual gas pressure is maintained on a rubber part, gas molecules can be absorbed into the rubber. This does not affect the rubber unless the pressure is suddenly released, at which point the entrapped gas tries to rapidly escape from the rubber lattice, often rupturing and exploding the rubber in the process. Careful polymer selection can compensate for this effect, typically encountered in Down Hole O&G applications. See also RGD, Rapid Gas Decompression, and our Blog on the subject.
Extending Flash
Flash that is formed at the parting line of a mould.
Extrudate
The product or material delivered from an extruder, for example, profiles, tubing, squares.
Extruder
A machine for producing more or less continuous lengths of rubber sections such as rods, sheets, tubes, and profiles, by forcing uncured rubber compound though a suitable die, and then curing the resultant section in an autoclave or microwave oven.
Extrusion
Of a seal – When a part or all of a sealing component is forced from its groove from pressure, or into a clearance gap between mating mechanical components in an assembly. Of a material – The generic term given to products such as rubber or plastic lengths of material produced by an Extruder with a continuous profile.
Fabricated Sleeves
Fabricated cylindrical or tapered tubes from a variety of rubber and composite materials, primarily used to connect pipes, finish the ends of discharge chutes or compensate for relative movement.
Fabrication
The process of joining parts, in the case of rubber by any of several methods including glueing, hot vulcanising or shot moulding. See also “Assembly”
Face
Front surface of a seal. See also “A” Face.
Face Seal
A sealing system in which the sealing occurs in the axial direction of the seal. If the seal ring were to be placed flat upon a desktop, the seal compression would occur between the top and bottom of the seal. See also Axial Seal and Static Seal.
Family Mould
A multi-cavity mould where each of the cavities forms one of the set of component parts of the finished assembly. This can lead to problems when unbalanced flow means that one item of the set does not mould as well as the other parts, resulting in unequal quantities of good parts.
Fatigue Strength
The maximum cyclic stress a material can withstand for a given number of cycles before failure occurs.
FDA
Abbreviation for Food and Drug Administration, the U.S. agency under the Department of Health, Education and Welfare which is concerned with the safety of products marketed for consumer use.
Feed Gate
The area or orifice where rubber is injected or transferred into a mould cavity. Various types are called Fan, Direct, Pinpoint, Tab, Tunnel, Jump or Ring.
Filler
A relatively inert substance added to a rubber compound to reduce its cost, improve processing or physical properties, particularly hardness, stiffness and tensile properties. Materials such as carbon black, clay, calcium carbonate, and silica are used to change the properties of an elastomer.
Finish
The surface texture of a finished article.
Flame Retardant
Having the ability to resist combustion. A flame retardant elastomer is considered to be one that will not continue to burn or glow after the source of ignition has been removed. Specific test standards are laid down by various industries depending on their specific requirements. Flame resistance testing requires a standard burner and fuel, which gives a flame of known characteristics. Rubber samples are then placed at a certain position in the flame and removed after an ignition period. The time taken for the rubber to self-extinguish is recorded with notes regarding after flow and any hot particles emitted by the sample at any stage.
Flame Retardants
Additives that reduce the tendency of rubbers to burn.
Flash
Excess rubber found on mouldings as a result of the moulding process, but which does not form a part of the moulding itself. This does not usually include feed gates but refers particularly to thin films of rubber formed at tool split lines or venting gaps. Can be removed by trimming. See also Cryogenic Deflashing.
Flaws
Surface imperfections that occur infrequently.
Flex cracking
The tendency of some materials to crack as a result of repeated bending or stressing at the same point.
Flex Life
The time during which a material can be expected to resist cyclical bending.
Flex resistance
The relative ability of an elastomer to resist the stress of constant bending.
Flexural strength
The ability of a material to flex without permanent distortion or breaking.
Flow
The ability of heated plastic or uncured rubber to travel in the mould and runner systems during the moulding process. The scorchiness or viscosity of a compound will affect its ability to flow, and feed a mould effectively.
Flow Marks, cracks or lines
Surface or structural imperfection due to the failure of the rubber compound to properly blend or knit with itself during moulding. Caused by insufficient masticating of the material within the cavity during the closing of the mould, especially an issue with compression moulding, and certain materials.
Fluid
A liquid or gas.
Fluid Resistance / Volume Swell
Fluid resistance is commonly measured by the effect of the fluid on the volume of the rubber exposed as a volume change (e.g. +100% indicates that the volume of the rubber has doubled as a result of exposure to the fluid, -10% indicates that the volume of rubber has decreased as a result of exposure to the fluid). Volume change is measured by determining the weight of a sample in air and water before and after exposure to the fluid under defined conditions. The sample is normally totally immersed in the fluid.
Fluoroelastomer
Often known as Viton® it is thought of as a super elastomer, however whilst it has excellent temperature and chemical resistance, it is relatively weak, does not perform well at low temperatures and is attacked by steam. Nonetheless, this expensive family of polymers is very useful and a variety of alternative versions exist with a combination of properties, although some of the more extreme versions are quite difficult to process.
Fluorosilicone
Similar in properties to Silicone rubber, having exceptional temperature range and good cosmetics, but with enhanced resistance to oils and fuels. As such it is not a particularly strong polymer, and is extremely expensive, so care should be taken to ensure that it is the most suitable material for any given application.
Foam Impact Protection Profiles
Impact protection foam profiles provide highly visible protection on sharp corners, edges, machinery, racking and vehicles – preventing accidents in the workplace.
Forcing frequency
The frequency at which an external force is applied to a part to sustain it at a constant “forced vibration’ i.e. with generator set running at 1500 rpm the forcing frequency is 1500CPM or 25Hz.
Forming
A general term encompassing processes in which the shape of rubber extrusions is changed to a desired configuration.
Formulation
The term used to describe a rubber “recipe”.
Fracture
The separation of a body usually characterised as either brittle or ductile.
Frequency ratio
The forcing frequency over natural frequency – see “transmissibility curve”. The bigger the ratio the better the isolation.
Friction
Resistance of motion caused by surface contact.
Friction (Break-out)
Friction developed in dynamic seal situations during machine start-up. When machine operation is irregular, O-rings tend to conform (adhere) to the micro fine grooves of surrounding glandular surfaces, requiring extra initial force to break them out of these micro fine grooves.
FRP
Fibre reinforced plastics.
Gasket
A deformable material clamped between two surfaces so as to prevent loss of material or pressure and to create a seal. A static (stationary) sealing device used to retain fluids under pressure or to seal out foreign matter when a deformable material is sandwiched and compressed between two mating surfaces.
Gate
In injection and transfer moulding, the orifice through which the melt enters the cavity. Sometimes the gate has the same cross-section as the runner leading to it; often, it is severely restricted.
Gate Mark
A raised spot or small depression on the surface of an injection or transfer moulded part where gates interface the cavity.
Gauge
Thickness of a sheet material. Or a dedicated jig to assess a limit or fit.
Geometric Dimensioning & Tolerancing
A means of specifying engineering design and drawing requirements with respect to actual function and relationship of part features. Furthermore, it is a technique which properly applied ensures the most economical and effective production of these features.
Gland
The space in a mechanical system into which a seal is installed. The gland consists of the seal groove and any additional space required for achieving the proper compression of the seal. Care should be taken to distinguish between the terms gland and groove, which are separate but related concepts.
Groove
The machined glandular recess into which an O Ring or Seal is fitted.
Groove Depth
The measured depth of a feature, frequently a slot, machined or otherwise created in a mechanical system to physically locate and constrain a seal. Care should be taken to distinguish between the terms Gland Depth and Groove.
Hardness
Resistance of rubber to distortion forces. Measured with a Hardness Tester in degrees and based on the resistance to penetration into a standard sized cured rubber sample of a defined indenter under a set load. Three scales are commonly used: IRHD (International Rubber Hardness Degrees), Shore A for standard solid elastomers and Shore D for hard materials over 90° Shore A. IRHD is preferred for most specifications but Shore A is also in widespread use. High values indicate harder materials while low values indicate softer materials. The Shore A and IRHD scales are similar but do not directly correlate.
HDT
Heat-deflection test.
Heat
One part or set of parts produced by one cycle of a moulding press. (Also see “lift”)
Heat Aging
Loss of physical properties as a result of exposure to heat over time. Also known as “accelerated ageing”. Rubber materials are often tested for shorter times at higher temperatures to predict what will happen over longer times and at lower temperatures.
Heat deflection temperature
The temperature at which a standard plastic test bar deflects 0.010 in. (.254mm) under a stated load of either 66 or 264 psi (4.55 or 18.2 Bar)
Heat Resistance
Rubber compounds capacity to undergo exposure to some specified level of elevated temperature and retain a high level of its original properties.
Heat Sealing
A method of joining plastic parts or films by simultaneous application of heat and pressure to areas in contact. Heat may be supplied by conduction or dielectrically.
Hermetic seal
An airtight seal.
Heteropolymer
polymer composed of differing monomers.
Hevea Brasiliensis
The commonly known “Rubber Tree” is actually correctly known as Hevea brasiliensis, or, in south america, the Pará rubber tree. It is the main source of latex, and from its origins in south america was transplanted by the British to India, Malaya and Africa in the 1870’s to establish an alternative source of latex for natural rubber production. Natural rubber is still sometimes called Para rubber due to its original source tree. Latex can also be harvested from other species of plant, such as the dandelion family.
HM
High-modulus.
HMC
High-strength moulding compound.
HMW
High molecular weight – typically of an engineering plastic.
HNBR
A very good synthetic having good moulding characteristics, better physical properties than Nitrile and excellent thermal and abrasion resistance, and good hot water and steam performance. It is relatively expensive, but finds applications in automotive drive trains, timing belts, cam chain tensioners etc., and has excellent resistance to explosive decompression, which makes it ideal for many downhole oil & gas applications.
Homogenous
A mixture that is uniformly dispersed. In finished seals a rubber seal without fabric or metal reinforcement.
Honing
A machining process that sharpens, enlarges, and smoothes material through the use of a fine-grit stone, typically used on piston bores to create the optimum sealing surface conditions.
Housing Size
The size of the metalwork containing a seal, being the space in which the seal is designed to operate.
Hysteresis
The difference between the amounts of energy absorbed when a rubber is stretched and the amount of energy released when the rubber is relaxed. High hysteresis indicates a high loss of energy (and so is good for energy absorbing applications). Low hysteresis rubbers are more resilient. Also refers to the build up of heat in an elastomer sample caused by rapid deformation.
I.D. (Inner Diameter)
The innermost (smallest diameter) surface of a circular object, such as a bore or a round seal, often an O Ring. The term I.D. is frequently used to indicate both the circumferential surface itself as well as the measured diameter of that surface.
Impact Resistance
Relative susceptibility of plastic products to fracture by shock or stresses from high speed impact. Indicated by the energy expended by a standard pendulum type impact machine in breaking a standard specimen in one blow
Inclusion
A foreign object or particle found to be present in a moulded part. Such defects can compromise the strength of a moulded part.
Inflatable Seals
Specially fabricated elastomer seals designed to inflate with air to form a tight barrier between two surfaces.
Injection Feeder
The cone shaped or tapered holes that feed down to the cavity area of a transfer or injection type mould. Elastomeric material is forced through these holes when the mould is under pressure. The rubber then fills the cavity area and forms the rubber parts.
Injection Moulding
The method of forming objects from granular or powdered plastics, most often of the thermoplastic type, in which the materials is fed from a hopper to a heated chamber in which it is softened, after which a ram or screw forces the material into a mould. Pressure is maintained until the mass has hardened sufficiently for removal from the mould. In the case of Rubber, the unvulcanised solid material is preheated and then injected through a series of runners into the closed cavity, where pressure and temperature is maintained until cure is achieved.
Injection Pressure
The pressure on the face of the injecting ram when injecting material into the mould. It is usually expressed as P.S.I.
Injection Ram
The ram or screw that applies pressure to the heated plastic or rubber material to force it into the mould cavities.
Insert
An article of metal, plastic or other material which is incorporated into a rubber moulded part either by pressing the insert into the finished moulded part, or by placing the insert in the cavity prior to moulding so that it becomes an integral part of the moulded part, either by simple overmoulding, or by chemical bonding during the curing process.
Insertion Rubber
A sheet rubber material with fabric “inserted” into the rubber to provide tear resistance. Used principally as a gasket or diaphragm material, “Insertion” can have various combinations of the number and type of layers of fabric and the type of rubber binding them together, depending on the application. Conveyor Belting is a specific example of this technique, where the longitudinal stiffness of the belt is provided by the fabric layers, whilst remaining flexible enough to pass around the drive rollers of the belt system.
Interference Fit
Where mating components, often metallic, are intended to have no clearance between them when fitted together, locking the parts together.
Internally Lubricated Rubber
A rubber formulation containing lubricating materials. An internally lubricated rubber is designed to reduce the coefficient of friction of the rubber material.
IRHD (International Rubber hardness Degrees)
A system of characterising an elastomer by its resistance to penetration of a known geometry indenter by a known force. This micro technique is reproducible on irregular as well as flat surfaces and on cross sections as small as 1mm in thickness (.04″). Measurements taken using the IRHD scale are similar, but not identical, to those obtained using the Shore A scale.
Ishikawa Diagram
Also known as the Herringbone diagram, a tool for Root Cause Analysis.
ISO
Abbreviation for Isocyanate, a major constituent used in the production of Polyurethane solid and foam products in conjunction with Polyol.
Abbreviation for the International Organization for Standardisation – model for quality assurance in design, development, production, installation and servicing.
ITAR
International Trade in Arms Regulation, the protocol applying to US controlled military products.
Jig
A tool for holding parts of an assembly during the manufacturing process.
JIT
Just in Time manufacture, a lean manufacturing technique developed by the Japanese automotive industry in the 1950’s to reduce inventory as far as possible.
K-Factor
A term sometimes used for thermal insulation value or coefficient of thermal conductivity.
KANBAN
Developed by the Japanese automotive industry in the 1950’s, designed to “pull” parts onto a production line only when needed, whether by cards or physical bins containing stock.
Kink
Deformation caused by bending or twisting a tube or profile so that it returns upon itself.
Knit Lines
Marks visible on a finished part made by the meeting of two flow fronts during moulding. When stressed, may result in a peel failure. See also Splits and Voids.
L/D Ratio
The term used to define an extrusion screw. This is the screw length to screw diameter ratio.
Laking
Surface markings resulting from the trapping of air between the material being cured and the mould surface. See also “Air Checking”
Laminar Flow
The flow of a resin in a mould is accompanied by solidification of the layer in contact with the mould surface that then acts as an insulator through which material flows to fill the remainder of the cavity.
Laser Etching
Physically making a component with a laser, often to uniquely identify each individual component with a unique serial number. Rubber products can be Laser Etched satisfactorily.
Latex
Natural colloid solution harvested by “tapping” from the Para tree or crushing other vegetable sources such as Dandelion and Guayule. It is then refined into the organic compound Isoprene, commonly known as “Natural Rubber”.
LCP
Liquid crystal polymer.
Leakage rate
The rate at which a fluid (either gas or liquid) passes a barrier.
Life Group
Shelf Life of rubber products can be established and controlled by “Life Group”, where packaging and storage conditions are laid down by polymer type. See BS 2230 for the various conditions and polymers covered by such a standard.
Life test
A comparison of the relative performance capabilities of various products or materials. This laboratory test determines the amount and duration of product resistance to multiple destructive forces or conditions. Samples may be standardised for universal comparison, or specific for bespoke testing and comparison.
Lift
The set of rubber parts resulting from a single mould cycle or pressing, created by the number of cavities in the mould tool. Also called a “heat”.
LIM
“Liquid injection moulding” is a closed manufacturing process using LSR in an injection moulding machine.
Load / Deflection testing
measuring the amount of load required to deflect a part by a given amount. Often a bespoke test of parts to determine whether the finished part or assembly is within design parameters.
Low temperature flexibility
The ability of an elastomeric product to be flexed, bowed, or bent at low temperatures without evidence of cracking.
Low Temperature Flexibility
The ability of an elastomeric product to be flexed at low temperatures without cracking.
LSR
“Liquid silicone rubber” is composed of a two-component, low viscosity, heat-curable rubber system.
Material Safety Data Sheets (MSDS)
Documentation regarding the toxicity or hazards associated with contact with some substances. These are prepared by the manufacturer of the substance.
Mating Surfaces
Points where different parts of an assembly meet.
Mechanical bond
A method of creating a moulded part where the rubber is mechanically attached to an overmolded insert through the use of holes, depressions or projections on the insert, thus requiring no bonding agent to create a chemical bond.
Mechanical Property
Properties of rubber and plastics which can be classified as mechanical include abrasion resistance, creep, ductility, friction resistance, elasticity hardness, impact resistance, stiffness and tensile properties, etc.
Melinex & Mylar®
Polyester film products typically supplied in gasket or shim form.
Melt Index
A measure in grams of plastic material that can be forced through an orifice of 0.0825 inches when subjected to a force of 2160 grams in 10 minutes at 190°C
Memory
The tendency of a plastic or rubber article to revert in dimension to a relaxed size previously existing at some stage in its manufacture, after deformation.
Metric Units
Milli Centi Deci Meters Liters kilo Deka Grams Hecto.
Micro hardness
A measurement of rubber hardness for specimen’s below .25 inches (6.35mm) in thickness. Micro hardness, like Shore A durometer, is also a measurement of indentation.
MIL STD
Abbreviation for Military Standard.
Mineral Reinforcements
Inorganic substances used as filler for rubber and plastics. Some common examples are: clay, mica, talc.
Minimum Specifications
The minimum values, usually of mechanical properties that a compound must meet by Quality Assurance prior to shipment.
Mismatch
Unequal or offset split lines leading to an asymmetric product, typically O-ring cross-sectional problems can be caused by this effect due to lateral errors in the mould cavity, also creating excess flash on parts.
Modulus
Derived from the Latin word meaning “small measure”, modulus is the ratio of stress to strain in the linear region of the s-e logistic curve. It is measured as the force per unit area required to extend a rubber to a stated percentage of its original length e.g. to 100%, 200% or 300%. It is often written as M100 = 3.0 MPa (i.e. modulus at 100% = 3.0 Mpa).
Modulus in Compression
The ratio of compressive stress to strain within elastic limits of the material.
Modulus in Flexure
The ratio of the flexure stress to strain, within elastic limits of the material.
Modulus in Shear
The ratio of shear stress to strain within elastic limits of the material.
Modulus of Elasticity
The ratio of stress to corresponding strain below the proportional limit of a material in tensile testing, as measured on a rubber specimen.
Modulus of Elasticity (tension)
Force which would be required to stretch a substance to double its normal length, on the assumption that it would remain perfectly elastic, i.e., obeys Hooke’s Law throughout the test. The ratio of stress to strain within the perfectly elastic range.
Modulus of Resilience
The energy that can be absorbed per unit volume without creating a permanent distortion.
Moisture Absorption
The pick-up of moisture from the environment by a material.
Moisture Marks or Welds
Marks on the finished part that are caused from moisture in plastics or resins and look like weld lines, but can appear in places not typical of weld lines.
Molecular Weight
The sum of the atomic weights of all atoms in a molecule.
Molecule
The smallest unit quantity of matter which can exist by itself and retain all of the properties of the original substance.
Monomer
A relatively simple compound, usually containing carbon and of low molecular weight, which can react to form a polymer by combination with itself or with other similar molecules or compounds.
Mould Bolster
A standard frame or plate set that allows for interchangeable cavity inserts of standard pattern to be mounted in it. Each Bolster insert can however have a different cavity cut in it to produce a range of different parts from the same basic moulding press setup.
Mould Cavity
Hollow space in the mould tool within which plastic or uncured rubber compound is shaped and cured to the desired shape of the product.
Mould Finish
The surface finish of the mould which imparts the desired surface quality to the finished moulded product. Special finishes such as leather grain, spark eroded or patterned can be defined from various standards, and applied by various techniques, such as acid etch.
Mould lubricant
A material sprayed in the mould cavity that eases the removal of the moulded rubber products. See also Mould Release.
Mould marks
Surface irregularities, indentations, or ridges on the moulded product due to marks in the mould cavity, or damage to the mould. Can also be caused by an accumulation of release agent or wax deposits from previous moulding cycles, all of which detracts from the design intent of the cavity.
Mould (n) or Mold
A hollow form or matrix having the features & detail required of the final component into which a plastic or rubber compound is placed and which imparts to the material its final shape as a finished article.
Mould register
Alignment of all the parts of the mould cavity, various methods including dowel pins, taper locks etc.
Mould Release
A lubricant or baked on coating used to coat the surface of the mould to enhance ejection of the moulded article or prevent it from sticking to the tool.
Mould Shrinkage
Dimensional loss in a moulded rubber product that occurs during cooling after it has been removed from the mould. See our blog on Shrinkage.
Mould (v) or Mold
To impart shape to a plastic or rubber compound by means of a confining cavity or matrix.
Moulding Cycle
The period of time occupied by the complete sequence of operations on a moulding press requisite for the production of one set of moulded articles.