What are the different types of rubber moulding?
Posted on 01/07/2020 Category: Rubber moulding
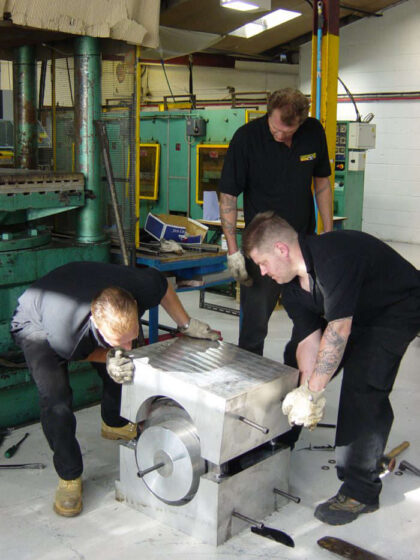
The process of rubber moulding takes raw rubber compounds and creates a final product in the desired geometry. An elastomer is a polymer with naturally elastic properties—meaning the moulded item will quickly return to its original shape after pressure is applied—and it is frequently used in industrial applications. There are several different types of rubber moulding processes, each with unique advantages, so read on and learn all about the types of rubber moulding from Martins Rubber.
What are the different types of rubber moulding?
When undergoing rubber processing, choosing the correct compound and manufacturing process is crucial to achieving the desired end result. By choosing the right moulding process for your application, you ensure optimum performance levels and cost-effectiveness.
There are three commonly used different types of rubber moulding:
- Rubber injection moulding
- Transfer moulding
- Compression moulding.
What is rubber injection moulding?
Rubber injection moulding, created in the 1960s as an extension of the plastic industry, is a process in which a heated rubber compound or material is injected into a closed mould under high pressure.
The rubber injection moulding process can be performed with a range of rubber materials, including silicone, neoprene, nitrile, and EPDM, enabling manufacturers to create a variety of moulded rubber products.
Advantages of rubber injection moulding
There is a range of benefits that come from rubber injection moulding, such as:
- Minimal material wastage
- Fast cycle times
- Fast production time
- High dimensional tolerances.
Disadvantages of rubber injection moulding
While there are many benefits of using rubber injection moulding, as with most manufacturing processes, there are some disadvantages:
- Increased setup costs
- Restrictions on the design of the tool and, ultimately, the finished part
- The requirement of more expensive tooling and machinery.
What is compression moulding?
One of the original and more straightforward moulding processes, compression moulding, combines heat and pressure to mould rubber into the shape of a metal tool. The rubber is shaped using a heated mould tool and the pressure of a clamping press. The curing—or vulcanisation—process occurs before the removal of the final part and cooling.
Advantages of compression moulding
Compression moulding has several benefits, including:
- Low levels of waste
- Simpler tooling and more cost-effective when compared to injection moulding
- Most suitable for parts with a large cross-sectional area
- Greater capacity to process stiff, high-durometer materials.
Disadvantages of compression moulding
There are only a couple of notable disadvantages of compression moulding, including:
- More difficult to maintain consistency of finished parts
- Slower processing times.
What is transfer moulding?
Last but not least, we have transfer moulding. The transfer moulding process starts with the raw materials being prepared as ‘pre-forms’ and then inserted into a pot internal to the mould tool. The mould is then forced through a runner and gate system and vulcanises upon introducing heat and pressure.
This process is similar to injection moulding since the rubber goes into the cavity after the mould is secured.
Advantages of transfer moulding
The advantages of transfer moulding include:
- Being more accurate and consistent than compression moulding
- There is a shorter manufacturing phase than compression moulding because multiple cavities can be used
Disadvantages of transfer moulding
There are several disadvantages to choosing transfer moulding, including:
- There is more chance of material wastage
- Inserted transfer moulding tools require repair time, removal, and reset maintenance
Designing the intricate moulds can be costly.
Find your rubber moulding solution with Martin’s Rubber
Ultimately, deciding which rubber moulding process is best for your application depends on the cost, time, and volume pressures. No one of the processes mentioned above is better than the other; they all apply to your requirements.
Here at Martin’s Rubber, we have 150 years of industry experience, and our rubber experts can provide the correct guidance and advice on which technique best suits your application. For all questions, be sure to contact us, or to learn more about rubber moulding, check out our technical articles.