Linear vs Nonlinear FEA’s
Posted on 14/04/2021 Category: Technical Features
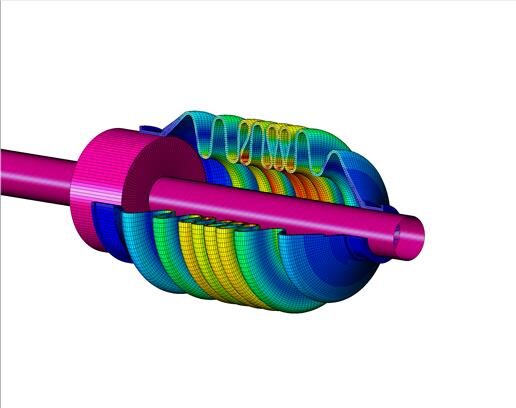
We often get asked what the difference is between linear and nonlinear FEA. Linear FEA is the perfect tool for the job it is designed for. But it is much simpler than nonlinear FEA. Learn all you need to know about FEA here at Martin’s Rubber.
What Is Nonlinear FEA?
A nonlinear analysis is needed when there is a nonlinear relationship between the forces and the subsequent displacements of a product or structure – in other words, within hyperelastic materials where the elastic deformation can be very large. In engineering terms, nonlinear FEA can relate to both material and geometric nonlinearity (such as high elongation). The stiffness matrix remains constant in a linear analysis until a predictable failure point.
A more user-friendly explanation? Linear materials such as metals can be evaluated with simpler equations; the response to stresses and strains is well documented and understood and can be easily predicted – this is FEA as most of us know it. As with all things, there are exceptions to this simulation technique, and, given our love of all things rubber-related, it will come as no surprise to you to find that we’ll be talking in more detail specifically about nonlinear FEA when applied to rubber materials and others that exhibit hyperelasticity, such as plastics.
Why Is Nonlinear FEA So Specialised?
The kind of engineering simulation facilitated by FEA has become a fundamental part of the design and development process in most product development cycles, and students leaving university now are generally familiar with linear simulation techniques. Even if (don’t worry – we won’t tell) you finished your degree before CAD packages that included linear FEA software were available, most mechanical engineers worth their salt nowadays know how to use standard FE analysis to simulate the performance of a component in situ.
Nonlinear FEA, however, is not often taught in most undergraduate engineering courses because such detailed knowledge of rubbers is required to conduct an accurate nonlinear analysis. So, if you’re wondering why your engineering team isn’t able to pull a nonlinear FE analysis out of the bag for a rubber component, don’t give them a hard time – it’s a pretty niche area!
How is nonlinear FEA used?
The basic reason behind performing either type of FEA is to simulate a product’s performance prior to manufacture or to understand why an existing product is failing in application. However, whereas most engineering teams will carry out their own linear FE analysis, the service is usually outsourced to those with expertise due to the specialism that non-linear FEA requires. We find that there are a range of reasons that engineers come to us wanting nonlinear FEA; the requirement usually falls into one of four camps:
To validate a design
This can be a justification for a project sign-off, release of funding or simply part of a standard engineering design process within an organisation to avoid unnecessary re-manufacture. If a similar part exists and is known to perform satisfactorily, then non-linear FEA may be called upon to demonstrate the (already known) likely performance of the new version.
To facilitate design improvements
Some customers are looking for us to work with them to redesign areas with a stress/strain impact. Others like to keep complete design control and request a report to make the changes in-house; we are then supplied with a new iteration of the analysis design.
Full design support
A component’s purpose and performance requirements are already well understood for some clients, particularly on parts such as boots, gaiters, and AV mounts for motorsport. In these situations, linear FEA is part of a complete design package; our customer provides us with a set of parameters and a space into which that product must fit, and we support them with a finished design, proven through simulation.
Failure analysis
FEA can be used to analyse a failure mode on a part that has failed in service and objectively assess and reverse engineer proposed improvements to the design or the materials used.
What is the difference between linear and nonlinear FEA software packages?
Linear FEA is included in most standard CAD packages and can be run once the modelling of a part is complete. Some CAD packages also include non-linear FEA programmes; however, in software such as SolidWorks and Autodesk, the options they provide only run to around 5% elastic strain. However, most rubber products will experience a more significant strain than this in application, making this functionality redundant for elastomers.
Software designed specifically for non-linear FEA rarely performs any other function; the mathematical modelling is complex enough that a complete package can be dedicated to this process alone. A significant amount of computer power is needed to run these simulations – the upshot is that they are neither cheap nor straightforward. There are software options available which don’t offer the option to visually review the calculated deformation modes, which can make curve fitting much more of a guessing game and can, therefore, introduce inaccuracies into the final result.
How does the user experience differ between linear and nonlinear FEA?
Whilst choosing appropriate software is critical to providing accurate outputs, the user must be able to understand and interpret those results. If you are unfamiliar with the expected curve fits for the deformation modes of a given material, or you lack the understanding of the bulk modulus, it is possible that one of the outputs could be wrong by a factor of ten. Not only would such a dramatic misrepresentation affect the overall result and what it tells you, but it wouldn’t be evident if you didn’t know what you were looking at because the correlation appears to make sense at first sight.
Find Rubber Manufacturing Solutions at Martins Rubber
There are no shortcuts if you are developing a rubber moulding and want to understand its performance before manufacturing. To get meaningful results, you must use the right software and fully understand your material. It’s a no-brainer; why wouldn’t you do the simulation up front and save time and money on manufacturing? If you’d like to know more about the difference between linear vs nonlinear FEA’s and how nonlinear FEAs could work for you, be sure to contact us or check out our blog and case studies for all you need to know.