The best type of bond; moulded – not glued?
Posted on 20/03/2013 Category: Technical Features
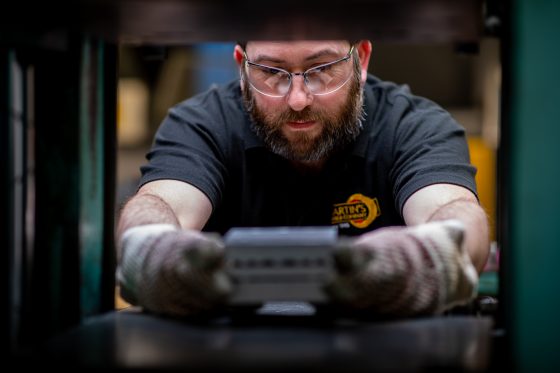
‘Off the shelf’ rubber products, such as sheet and extrusions, often need to go through a further process to create a final a product before it is ready for use in its intended application. For example, you may need to join separate pieces together, such as taking an extrusion and creating mitred corners to provide a finished seal in a square shape. Or you might wish to join a piece of extrusion or o-ring cord into a ring. These options might be used to create a product to be used in applications such as oven door seals, dock gate seals, boot and lid seals – where a fully moulded product is either unnecessary or impractical, but a fully formed seal is still required. A similar requirement for fabrication often arises for rubber sheet; it can be cut to length and joined as a cylinder to form protective sleeves, or in a conical profile to create products such as mast boots for the marine industry. To glue or not to glue? The first thing we should say is that very good adhesives are available, and can offer very strong bonds both rubber-rubber and to other materials. So, why would you choose to vulcanise a joint rather than simply glue it? The key lies in the application and the environment; adhesive joints will not necessarily withstand agressive temperatures and pressures, will break down under contact with particular chemicals, and are not always waterproof. Vulcanised joints can also provide a better finish aesthetically. How is a vulcanised joint created? Firstly, you need to cut the profile of the rubber material in order to form the most robust bond – a straight cut perpendicular to the surface would not usually achieve this. A dovetail joint may be the most effective solution. Next up, the material needs to be prepared – this would usually include a mechanical preparation, such as buffing:
Buffing rubber in preparation for bonding
A liquid compound is then applied to the joint in preparation for vulcanisation:
Application of a liquid compound to rubber in preparation for bonding
A jig or a full mould tool may be required in order to hold the two parts in place during vulcanisation if it is a profiled extrusion or a complex joint. The joint is then put under heat and pressure in order to cure the rubber and form a checmical bond through vulcanisation.
The joint is heated in order to enable a full bond
This method of joining will provide a different type of bond than using an adhesive alone, and the application should be assessed in order to establish what type of joint is required. This method of joining will produce a good bond, but dimensionally will not offer as tight a tolerance on finished dimensions as a fully moulded product would – but of course this may offer a cost and time saving, depending on the product and the quantities involved. You should also keep in mind that, if joining and bonding an extruded product into a ring, some profiles will not produce a consistent and useable product if the ID is particularly small or the profile deep. If you are unsure of which is the best manufacture method to use for your application, get in touch with one of our sales team who will be able to advise you on your options.
The post The best type of bond; moulded – not glued? appeared first on Martin’s Rubber Company.