Why Buna-N Is So Popular for Use With Hydrocarbons
Posted on 26/08/2023 Category: Latest News
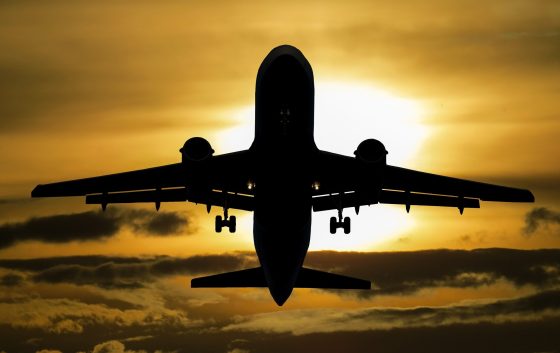
We love a novel material at Martin’s Rubber, something that has been specifically developed to do a very challenging job under a range of unusual conditions. However, our objective is never to unnecessarily reinvent the wheel or overengineer things.
Some fantastic rubber materials are already on the market and work perfectly for many industrial applications. Buna-N has been around for nearly a century and pulls its weight as a veteran of materials. But it’s important to understand what a material is good at and why.
If you’re looking for a rubber compound that is suitable for contact with hydrocarbons and that will provide great heat resistance and stability, Buna-N is likely to be at the top of your list.
Is Buna-N the same as Nitrile?
Buna N is a trade name for nitrile butadiene rubber (NBR), and BASF owned the name Buna N during the twentieth century up until the nineteen eighties. Buna-S was simultaneously developed in the US during the 1930s and is fundamentally the same compound, designed as a synthetic alternative to natural rubber. Nitrile rubber, or NBR, as it is most commonly known, became one of the most popular rubbers in circulation (notwithstanding natural rubber, used globally for tyre manufacture).
Why is Buna-N rubber so popular?
Buna-N’s chemical compatibility is its most valued property, widely favoured for its resistance to oils and fuels. It is the elastomer of choice for many automotive and mechanical aerospace applications – not only is it a practical rubber grade for fuel resistance, but it also offers good heat stability. It will withstand temperatures up to 100˚C or 120˚C in hot air applications. In aerospace and other industries, nitrile rubber is often found in automotive applications. It is popular for oil-resistant seals and diaphragms, fuel lines and other components that may come into contact with hydrocarbons.
Why is Buna-N resistant to hydrocarbons?
Due to the presence of acrylonitrile (ACN) in the polymer backbone, nitrile rubber (NBR) provides resistance to non-polar fluids such as hydraulic oil or petrol/diesel fuels. The level of acrylonitrile can vary in different grades, and the higher the ACN content, the poorer the low-temperature resistance and flexibility. However, those grades with the highest ACN content allow the highest resistance to swelling in hydrocarbon fluids.
Weaknesses of Buna-N
No rubber can excel at everything; to provide resistance or strength in one area, it is almost inevitable that another property will be compromised due to the careful chemical balance that must be maintained within rubber compounds. Due to its chemical structure, NBR has poor resistance to UV, ozone or weathering. This can be improved by using the saturated version of NBR, hydrogenated nitrile butadiene rubber (HNBR) – though this comes with a higher price tag.
Blends and Alternatives
Blends with PVC can be used for improved resistance to UV; however, this comes at the expense of elastic return, so it is not recommended for many sealing applications. The introduction of PVC into the NBR structure increases the material’s stiffness while lowering the elongation-to-break.
The benefit of this blend is the additional resistance provided by PVC, allowing for high-gloss cosmetic finishes and increased UV and ozone resistance without compromising oil and fuel resistance. PVC also significantly increases the range of applications for using NBR in cabling, allowing the NBR-PVC material to operate at higher temperatures. However, PVC is becoming increasingly regulated, so it now has a relatively high administrative burden.
If the level of oil resistance required is relatively modest, but the need for UV resistance is high, then neoprene can be a good alternative where mechanical properties are not critical; neoprene has the equivalent of a low-level ACN NBR, but HNBR would generally be considered a better alternative.
Availability of Nitrile Butadiene
Nitrile rubber (NBR) is one of the materials we use most commonly at Martins Rubber. Over a quarter of our rubber mouldings are manufactured in either NBR or HNBR. NBR is now readily available without the issue of material shortages.
Nitrile for Rubber Moulding
Nitrile rubber (NBR) can be used for all three of our moulding types – compression, injection, and transfer – without any difficulties. It is also widely used by our aerospace and motorsport customer base.
Nitrile butadiene rubber is one of the most useful general-purpose compounds in circulation for applications where hydrocarbons are in contact. It has weaknesses, and these can be addressed by using HNBR or by considering a more bespoke compound that may offer a more specific range of properties.
But, if you select NBR as your material of choice, you’ll be in good company. You’ll be choosing a compound that is great for moulding and will provide you with a product that can be manufactured consistently and reliably.
Contact Us
For all your rubber moulding needs, trust Martin’s Rubber to deliver the best results for your application. Explore our technical articles and case studies for more information on Buna-N vs Nitrile. If you have any questions about our rubber services, be sure to contact us; a team member will be happy to help.