How to Find the Tensile Strength of Rubber
Posted on 09/08/2021 Category: Rubber Testing
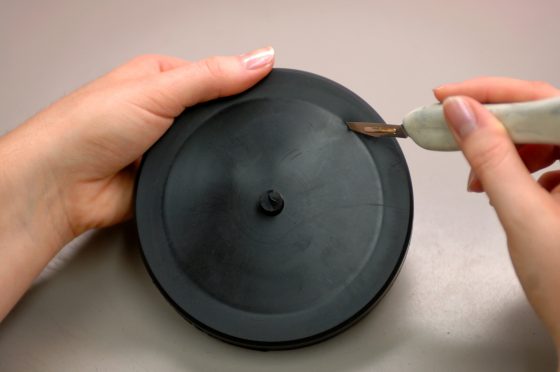
Tensile strength is one of the key factors that should be considered when selecting the right rubber material for any application, particularly where a rubber component plays a part in sealing, supporting, or anti-vibration. Tensile strength is often one of the main priorities in terms of material properties because it influences the performance of a product, especially where that product is likely to be under tension.
Here at Martins Rubber, we look at how to find rubber’s tensile strength, which factors influence it, and how it relates to FEA simulation.
Why is the tensile strength of rubber important?
Tensile strength is the property of a material that quantifies the maximum load it can withstand before fracturing. It applies to stiff materials such as metals, composites and natural materials like timber and stone just as much as it does to rubber. When a load that is less than the tensile strength of a material is applied, that material may deform or stretch but should return fully or mostly to its original size and shape. As the tensile strength approaches its maximum load, the material may begin to ‘neck’, showing a permanent deformation. As the load increases further, the neck will ultimately snap.
The tensile strength of rubber is unique to its chemical composition and structure. This particular property is important precisely because rubber’s elastic element is often the reason why it is the chosen material for an application—if you want a rubber seal surface to remain in contact with a shaft, a strap to retain its grip, or an AV mount to deliver long-term reliable support without snapping, then rubber provides the ideal solution.
How does the tensile strength of rubber impact product performance?
If your application requires support, grip, flexibility, or sealing, rubber is often the ideal material for the job. Therefore, it is important to consider how the rubber might fail under your specific operating conditions and what is required of the material to operate reliably.
Applications and environments can vary widely, and factors such as whether the rubber will be in compression or tension could be critical; a static pad that simply takes a long-term load may not need much tensile strength but will need good compression set properties, whereas an AV mount that could see both tension and compression cycles, as well as vibration, will need a much higher tensile strength threshold.
How to find the tensile strength of rubber?
A standardised industry-wide test is generally used to obtain a rubber material’s tensile strength. A standard-thickness sheet has a piece of rubber shaped like a dumbbell cut out using set dimensions. This dumbbell sample is then gradually stretched apart until it breaks. The force applied and the resultant elongation are plotted, and this stress/strain curve derives the Young’s modulus of the material.
This test also provides the ultimate measure of elongation at the point at which the material breaks; this informs us how much a given rubber will stretch before failure. Although this ‘elongation at break’ figure doesn’t relate directly to the material’s tensile strength, it is still a key value when calculating likely performance.
How does the tensile strength of rubber vary between different types of rubber?
A rubber’s tensile strength can vary widely depending on the compound in question; the differences in the structures of the polymer chains and their crosslinks give a broad range of tensile strength values and elongation at break values. As ever with rubber, there is an almost infinite mix of variable properties that need to be considered for the best performance in any given application, of which tensile strength is only one – which may not be the most important material property for some applications.
Can you alter the tensile strength of rubber to suit the application?
It can influence rubber’s tensile strength by selecting the optimum polymer type, cure system, and fillers. However, the tensile strength of a rubber may need to be compromised to ensure that a requirement relating to another property, such as hardness, temperature, or chemical resistance, is met.
How do you test the tensile strength of rubber for an existing product?
To understand the tensile strength of an existing rubber component, a test piece in the actual material used to manufacture that product would have to be created. This can be done by moulding a sample sheet under the correct cure conditions from the correct compound, and then a set of dumbbell test pieces are made and put through the test process described above.
It is not possible to establish information about this property from a non-standard shape, although empirical comparative testing could potentially indicate better or worse performance.
How does tensile strength relate to FEA?
FEA is used to simulate the performance of a component in situ, analysing likely failure points and providing the ability to improve a rubber product design before rubber manufacturers create it. One of the key pieces of data required for FEA is tensile strength; without knowing the tensile strength value of the rubber material intended for manufacture, it is impossible to calculate the failure point of a model being analysed under FEA. This is true of FEA for both linear and non-linear materials. Still, non-linear analysis needs additional information, such as a fully representative stress-strain curve and the type of failure mode – of which tensile stress failure is only one.
Find rubber strength solutions here at Martins Rubber
If you would like to know more about the tensile strength of rubber materials that you are considering working with or are considering likely failure points of a rubber component, be sure to get in touch. Whether it’s rubber development you need or expertise in non-linear FEA, we will be able to support you in finding the right material for your application.
Be sure to explore our technical articles and case studies for more information on finding rubber tensile strength. If you have any questions about our rubber services, be sure to contact us, and a member of our team will be happy to help.