Latest investment in rubber testing equipment
Posted on 28/01/2020 Category: Latest News
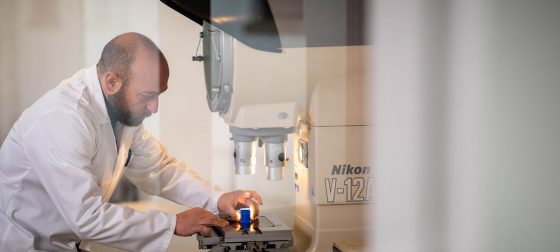
A moving die rheometer (MDR) provides us with the facilities for testing the characterisation of rubber curing, for both quality control and in our research and development work. This type of rubber testing provides the foundation for reliable and repeatable processing of materials and allows us to ensure consistent, high quality products every time.
What is an MDR?
An MDR, or Moving Die Rheometer, is apparatus for testing the viscoelastic properties of rubber compounds before, during and after cure. This machine provides information on the curing behaviour of rubber materials.
Why is an MDR important for rubber moulding?
MDRs provide a standardised rubber testing method for characterisation and control of rubber curing properties. With this rubber testing equipment, we can ensure the raw material is conforming at goods-in, and prior to producing any parts we can ensure the material is consistent and is within a set of controlled parameters.
This information is invaluable for quality control of materials, process control during the manufacturing of products, and is just one of the types of rubber testing used in developing and checking new materials in research & development projects.
MDR data, or rheology, gives information on the curing characteristics of that material. It is primarily used for testing rubber for batch to batch consistency and can be used to ensure the ongoing repeatability of a material.
The MDR allows us to run our own quality assurance checks on receipt of compounds. It also allows definitive shelf life testing of warehouse product as well as the ability to suggest informed process parameter modifications and apply greater control over process and product variation.
Our MDR rubber testing equipment allows for better product consistency with less likelihood of delivery delays due to unforeseen material shortages from stockholding and supplier error.
How is an MDR used for rubber testing?
In an MDR rubber testing process a standard heated die is filled with a precisely cut blank and then closed, whereupon the machine clamps the mould shut and starts a cure cycle, simultaneously oscillating the die halves rotationally, and measuring the torque transmitted through the rubber as it cures off. The shape of this torque curve, over time, gives us all the information we need about the curing characteristics of the particular sample, and will inform decisions about incoming material readiness and consistency across batches, the remaining shelf life of materials in stock, and the correct processing conditions for that material to maintain product consistency across a batch or history of production.
To obtain the best performance from the MDR rubber testing equipment, samples must be cut to an exact volume and shape to ensure the die cavity is filled with only the correct amount of material for the test.
Too little material and slippage can occur, affecting the test result. Too much material may cause the platens to not close & seal correctly, resulting in imprecise outputs.
To ensure only the correct volume of material is prepared for testing the rubber, a volumetric cutter is used to first compress the material to the correct thickness and then a cutting action takes place to measure an exact and constant sample volume.
Interpreting the results of the MDR rubber testing
The MDR data shows various data points from the rheology trace, an example of which is shown below:
A guide to the values:
- Min (or ML) – the minimum torque measured, gives an indication of the viscosity of the material
- Max (or MH) – the maximum torque measure, gives an indication of the cured stiffness of the material
- T05 – time taken to 5% cure, gives an indication on flow time to fill cavity
- T50 – time taken to 50% cure, usually the minimum amount of cure for dimensional stability
- T90 – time taken to 90% cure, good indication on the time to fully press cure a part
- PRT – time taken for the slop to reach its peak rate
- PR – the peak rate of the cure
We can measure the following properties of our rubber compound using MDR:
- Elastic torque curve
- Viscous torque curve
- Tangent delta cure time
- Cure rate time & values
- Scorch time
- Cure percentage
- Programmable data points & limits
- Pass/Fail limits – time or cure gates
Our rubber testing equipment is critical to ensuring that you receive consistently high quality products. It also provides us with the facilities for various types of rubber testing during our research and development of novel materials. If you would like to know more about our test facilities or developing a specialist compound that will work in a specific environment, get in touch today on 023 8022 6330 or [email protected]