Rubber Moulding Quality Control… the black art
Posted on 22/07/2013 Category: General Martins Rubber blog
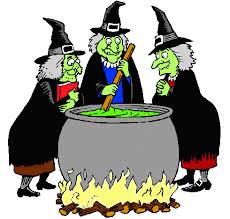
When entering the rubber industry one of the first comments I heard is that the control of the manufacturing process is a “black art”. Naturally, as the person ultimately responsible for assuring the delivery of consistent products to our customers hearing that the process is controlled by some magical force that only the operators understand left me feeling a little uneasy… of course as time has gone on and I have grown to have a greater understanding of the process I have discovered that there is actually very little that is not controlled by the 3 main parameters of the rubber moulding process.
Time:- The cure time, while critical, is easily controlled as cured rubber has a tipping point before which the rubber remains in an uncured sticky mass, and for certain types will revert and again to become a sticky mass, therefore the time can be easily determined by making sure enough is given without going beyond the acceptable time limits for efficient productivity. Temperature:-To vulcanise properly rubber compound needs to reach and be maintained at a temperature sufficient to energise the molecules into forming the cross links that create the finished product. In conjunction with time, temperature can be varied within limits to suit the product being moulded. As with time, too little temperature and the part comes out under cured; too much temperature and the rubber can be scorched or revert. Pressure:- This is used to regulate the flow and swell of the compound during the moulding processes and can have a significant effect on the final outcome of the moulding. While not directly linked to time, variation in pressure can be used in conjunction with variation in temperature to alter the overall moulding condition. When related to a tool it is important that sufficient pressure is applied to shut off correctly or the dimensions of the finished product will be affected. The skill in the application of pressure is that it is not always desirable to apply a constant pressure throughout curing and this is where the control of this element becomes critical. Understanding these parameters and their inter-relation enables us to set limits that in other manufacturing processes would seem uncontrolled but provide a stable and repeatable product. With rubber we have the luxury that you either have a solid mass or a sticky mess depending on whether it is correctly cured or not. The skill, the black art if you like, is in fine-tuning these parameters to make the parts in the most efficient way with the least number of rejects.
The post Rubber Moulding Quality Control… the black art appeared first on Martin's Rubber Company.