Importance of testing rubber: 4 reasons rubber products fail
Posted on 23/12/2019 Category: General Martins Rubber blog
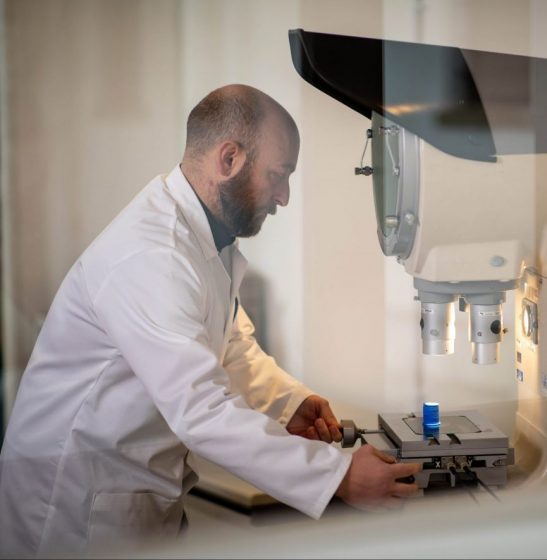
Proper rubber testing is essential to avoid catastrophic failure within heavy-duty manufacturing applications. Although rubber is known for its tough, elastic and durable characteristics, it is still susceptible to failure. That is why proper analysis and fatigue testing prior to use is so important.
In this article, we take a look at four of the common reasons why rubber products fail, why it happens and how the rubber testing methods at Martin’s Rubber can help to avoid them.
Four reasons rubber products fail
- Time and temperature dependency – When rubber is chosen for use it is nearly always with longevity in mind. It is therefore important for us to understand the operating conditions and temperatures that the application encounters on a daily basis. Rapidly increasing temperature demands that occur on a regular basis will compromise the fatigue life of rubber compounds.This will inevitably lead to the failure of the rubber product being used, which is why proper materials testing and fatigue testing needs to take place. Without testing, the outcome of your rubber product failing could be catastrophic.
- Negatively affected by the operating environment – One of the main causes of rubber fatigue is environmental influences. When coming into contact with chemicals and/or other such corrosive substances, the long-term condition of rubber can be affected and ultimately it will fail if the choice of compound was not appropriate for the environment.Effective rubber testing can help to avoid this as it will ensure you are using the right compound with the right characteristics. The use of a high-quality fatigue testing process will recreate the applications your rubber product will be working in, replicating important factors such as strain, crack growth and crack nucleation.The end result is that you will be left with a highly accurate idea as to how your rubber component will perform for its specific application prior to using it.
- Mechanical Failure – There are two types of mechanical failure when it comes to rubber manufacturing: ductile failure and brittle fracture. Ductile failure occurs when the rubber material is under high strain and begins to crack. The cracking of the material usually progresses slowly, with deformation of the rubber occurring alongside this.Whereas ductile failure occurs under high strain, brittle fractures are characterised by failure at low strain. In the instance of brittle fractures, there are little or no signs of deformation. Small crack-like defects tend to occur and these grow as the load they are working with increases. As this progresses within the rubber it can lead to rapid failure.
- Poor material choice – Materials testing is vitally important to ensure the rubber you are using has the characteristics to handle the performance requirements of the application. Here are some examples of the characteristics that should be considered when choosing your material.
- Thermal properties – It is important to define whether your material can handle the temperature demands of your application, especially if it is required to be fire retardant.
- Mechanical properties – This includes checking the compression set, hardness and the tensile strength required of the rubber. Tensile testing of rubber will ensure that the material you have chosen can withstand the stress and forces it will come under before it breaks.
- Electrical properties – Making sure that your materials have the right levels of conductivity or resistance for the application they are working with is another way to avoid poor material choice.
- Environmental properties – Choosing the wrong materials for the application and the operating environment can also lead to the rubber failing.
Testing rubber with Martin’s Rubber can help you avoid failure
If you are looking to understand how your rubber product will work and how it will wear, then Martin’s Rubber can help you. Using expert rubber analysis and validation – either through practical, real-world testing or simulated environments – Martin’s Rubber has the capability to support your material choice.
For more information about our rubber testing techniques and practices, visit the rubber testing section of our website.