How does FEA calculate stress?
Posted on 17/04/2021 Category: Technical Features
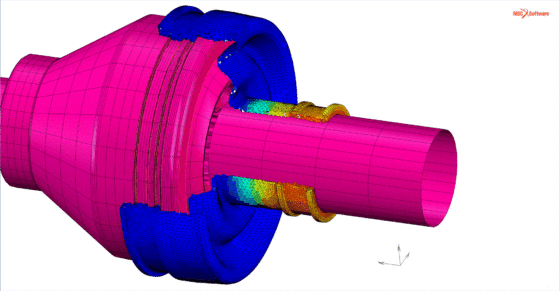
We’re all now pretty familiar with the kind of stress that can make you want to throw your laptop out of the window following a frustrating Zoom call – we can’t really help with that (although we promise a video call with us won’t end that way!) However, stress in engineering components can result in their premature failure.
Stress refers to forces acting upon the component, and strain describes how that component deforms relative to its undefined state in response to the stress. You may want to know whether the rubber material that you’ve selected for a design is up to the job. If so, it is critical to consider the nature of the material’s stress-strain relationship in relation to the application conditions.
Finite Element Analysis (FEA) can be used to investigate how your product will behave. The stress-strain relationship is a fundamental factor within FEA calculations, and here we take a more detailed look at how FEA calculates stress and strain in engineering components.
How does FEA calculate stress in linear materials?
Ok, let’s dust off our school GCSE maths and physics and get down to some basics for just a moment. The assumptions that linear stress calculations use look like this:
stress = force / area
and this assumes that…
force = stiffness * displacement
Therefore the component’s response to stress is dependent on both stiffness and geometry, and the properties of the material impact this calculation from the outset.
In order to assess how a component will respond to stress, we also need to understand the strain that the product will exhibit. Strain is defined as the change in size/shape of the original item and is calculated like this:
strain = change in length / length
For materials that can be modelled using linear FEA, the relationship between stress and strain is itself linear, until the point of failure – termed UTS (ultimate tensile strength). This linear relationship is defined by Young’s modulus (the elastic modulus), which says that:
modulus of elasticity = longitudinal stress / strain
This relationship dictates the slope of the graph produced for the stress/strain relationship.
In many materials, any deviation from this linear response will be characterised as failure; either fracture or permanent plastic deformation, where the part will no longer return to its original form. From that point the Young’s modulus no longer applies.
Nonlinear hyper elastic materials, such as rubber, can withstand much higher levels of deformation (higher levels of strain) before failure. It is important to note that for these materials the stress-strain relation is more complex and cannot be described using values such as Young’s modulus to obtain results above small strain.
Still with us? Good, because now we move onto nonlinear FEA, where we pick up the pace a bit.
How does FEA calculate stress in nonlinear materials?
Nonlinear FEA can use several different equations to describe the stress-strain relationship. Nonlinear FEA uses empirical data and complex equations to simulate the shear, tension and bending stresses. The software calculations use a series of vector equations to model the behaviour of a component under stress. It then combines these directional and deformation responses into an overall stress response. The outcome of the analysis can be provided in terms of von Mises stresses and elastic strains, among others.
How is the input data gathered for FEA calculations?
To provide material constants which allow the mathematical modelling to be as accurate as possible, nonlinear FEA packages use a curve-fitting process which is based on stress-strain data from physical tests. These tests can include:
- Uniaxial tension or compression
- Planar shear
- Equibiaxial tension
- Volumetric compression
Although the software can be run using results from just one of these physical tests, the greater the data input, the more accurate the simulation and therefore results.
The stress analysis in nonlinear FEA, just as in linear FEA, is only ever as reliable as the set-up and the analysis process. Because nonlinear FEA has a directional dependency, we have to operate in three different modes to complete an overall analysis: simple tension, pure shear and equibiaxial curves. Most analysis is based on an empirical uniaxial input, and then a mathematical curve fit. This means, in the absence of full test data, the software calculates a predicted response in the other deformation modes.
The more deformation data that we have, the more accurate the output and the more scope for validating the result. In order to achieve the highest possible accuracy, it is critical that we test the actual material to be used.
How do we ensure that your nonlinear FEA results are accurate?
As rubber and FEA experts, we apply our expertise alongside the software to ensure accuracy is achieved even in the case of limited empirical data. In addition, if any assumptions are to be used we ensure these are detailed and agreed with our customers in advance. We aim to work with as full and accurate a data set as possible, using data that most closely suits the component’s operational stresses.
To scope a potential project using nonlinear FEA we initially review the design and the application conditions and requirements. The scoping ensures we can establish what exactly can be checked, measured and controlled – for example, what pressures and loads will be used, the level of friction that the part will experience, which materials and associated properties to test against. From there, we discuss what kind of output or information is most valuable, and make recommendations around those needs.
Wanting to understand how FEA calculates stress does take you down a rabbit hole both in terms of the complexities of hyperelastic materials and also how mathematical modelling can be applied differently when used in a computer-aided simulation with, quite frankly, far more brain power than any of us could muster on an average day. But it is an important question because it gives some idea of the kinds of decisions, knowledge and assumptions that need to be made to provide you with the most accurate results possible.