AS9100 for SMEs: an expensive tick-box or the road to success?
Posted on 23/02/2023 Category: Latest News
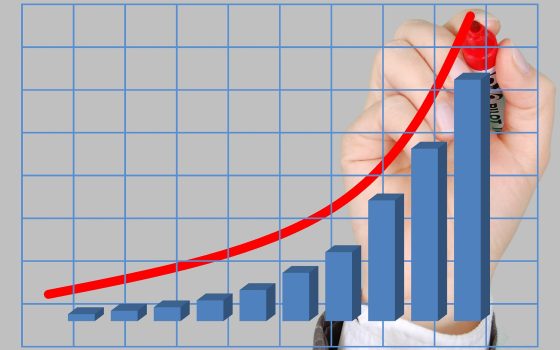
Our quality manager describes AS9100 as ‘ISO9001 on steroids – but in a good way’. AS/EN9100 is a quality standard used within the aerospace, space and defence industries; developed by the giants of aerospace, it was designed as a kind of insurance policy, with standardised requirements that they all agreed they wanted to roll out to their contractors and onward throughout the supply chain.
With a greater focus on risk-based thinking, AS/EN9100 forces the business to focus on areas of weakness, strengthening them and slowly pushing all parts of the business to perform with greater consistency and at a higher level. Internal auditing prioritises high-risk areas, with a requirement for an improvement plan and then more regular assessments. Goals for improvement are challenging but achievable, with targets that are stretched as they are met, ensuring continuous improvement. Unlike ISO9001 which selects just a few areas to audit on each external auditor’s visit, AS9100 auditors look at every area of the business and its processes each year.
If you’re thinking that this sounds arduous and like a lot more work than ISO9001, in a way you would be right. However, the increased workload, for us, has shown more than a relative improvement for the business. We’ll take a look below at some of the ways in which AS/EN9100 has benefited our customers, how it has improved our own business practices, and then look at the cost implications for those who are considering starting out on this journey.
How our customers benefit
- Consistency of service. As a manufacturer we have always had processes in place for making things. However, the introduction of AS/EN9100 has made us look much more closely at the processes outside of the manufacturing areas:
- Quotation calculation and creation now has a much more stringent process, ensuring that our costs are likely to be both more accurate and more consistent.
- Sales order loading processes have been updated, demonstrably reducing administrative and system errors.
- Packing and shipping processes are now much more uniform so that we provide a more effective and more streamlined shipping service.
- Overall contract review is much more robust. This means that we ensure from the outset that we understand customers’ needs fully, document what, when and how we’re agreeing to fulfill the solution, and then deliver to our promise.
- A uniform approach. We now have a much more consistent level of service throughout the business; best practice is based on quantitative data to demonstrate effectiveness and then rolled out across all personnel and all teams.
It may sound obvious that all these things are important, but it’s easy within a growing business to have departmental differences in approach, and the people within those teams creating a methodology that suits them, rather than one that is best for customers. Without a really stringent set of processes, customer experience can vary from order to order, and that’s the area in which we’re really seeing change happen.
How we’ve benefited
- Consistency of operation and methodology. Processes throughout the business are better controlled and documented. A much wider set of work instructions create a more uniform
Zygi Navickaite, Quality Manager
approach, which not only helps control consistency but also makes it much easier to train people. And in a business where we need people to be multi-skilled, and where many of our products are custom-made, the more uniformity we can achieve, the better for our customers and for our own bottom line.
- Everyone is held accountable. AS/EN9100 is designed so that not only are the Quality Team responsible for quality of service and product, but so is each person within the business. Our company now has a noticeably more positive quality culture, one where everybody understands its importance and is actively engaging with the process of developing and maintaining those standards.
- Empowerment for resolution. Where issues arise – either as a customer complaint (let’s be honest, we all have them!) or a problem with an internal process – the improved quality culture means that people are much more empowered to find a solution not just for the short-term, but also to prevent a recurrence.
- Process changes are much more widely understood and considered. Whilst updating or amending a process in one area may apparently solve the issue, unless impacts on other departments and their processes are considered, there may be an unintentional knock-on effect elsewhere. AS9100 has led to a much better appreciation of the broader impact of process change throughout our teams.
- Reduced scrap rates through consistency of manufacture. Rubber manufacture inevitably produces a level of scrap and this is accepted across industry. However, AS/EN9100 encouraged us to look at scrap rates from new angles, and has already resulted in further improvements to both profitability and our environmental footprint.
- Improved customer service. The benefits of the improved service outlined in the previous section really speak for themselves; a stronger order book and repeat business are the cornerstone of any company, SME or otherwise.
But what about the investment?
Time and commitment. It’s true, AS/EN9100 shouldn’t be taken on casually; it’s a big project from the get-go and needs proper support from throughout an SME, with the risk of failure creating a stress-point in what is often an already stretched team. Added to that, as an ongoing commitment there is the requirement for 5 external audit days per year (vs the two for ISO9001), where all processes will be audited. Suffice to say, AS9100 isn’t a quality management system for those who just want to pay lip service and get a tick in the box.
The initial preparation to ready ourselves for the initial AS/EN9100 audit took a year or so – and involved every departmental manager and their team, lead by a Quality Manager who has experience in working with the AS9100 standard. We were lucky enough to have a senior management team who were keen to drive the project forward and understood the likely benefits to the business.
Open to inspection. AS9100 approved businesses must sign up to an open database called Oasis – a portal that logs your performance across all areas, including any failures or non-conformities. Depending on your size and place in the supply chain you can see all or some of this information about your customers, suppliers and competitors – so AS/EN9100 is not for the faint hearted as you have to be willing to be completely open about any areas of weakness, and be seen to be addressing them.
Measurement and accountability. AS/EN9100 requires every business to measure key processes. You need to have the means to measure, record and improve on each of those areas consistently. Our core areas, which each have two KPIs against them, are:
- Sales: Turnaround time for quotations, accuracy of information
- Technical support: number of internal complaints raised, speed of quotation process
- Purchasing: supplier delivery to promise, supplier concerns raised
- Manufacturing: scrap rate, completion of orders on time and in full
- Despatch: number of internal complaints raised, shipping of stock on time
Any regrets?
The subsequent culture of honest debate and teamwork created by the implementation of AS/EN9100 has led to a stronger and more robust foundation for Martin’s Rubber to operate upon.
As pointed out by our Quality Manager, Zygimante Navickaite, AS9100 doesn’t necessarily have to add extra work and administrative burden to every team; if people are willing to be creative and find new ways of approaching a problem, often the result can be a more streamlined and effective way of doing things – but it does mean allowing people the time and space to think things through and be open to alternative ways of working.
Overall, is AS/EN9100 working for us? Absolutely. In our experience, ISO9001 works well for quality departments, but AS/EN9100 improves the business overall. When we set out on this journey, we knew we wanted to improve our operations to make it a more robust, more efficient and more sustainable company to allow for growth, whilst also providing our customers with a better service. We chose to benchmark ourselves against a standard that holds us accountable to that ethos, but the mindset was already in place and that may just have been the key to success.