Rubber compound shortages: a global phenomenon
Posted on 10/05/2022 Category: General Martins Rubber blog, Martins Rubber News, Rubber moulding
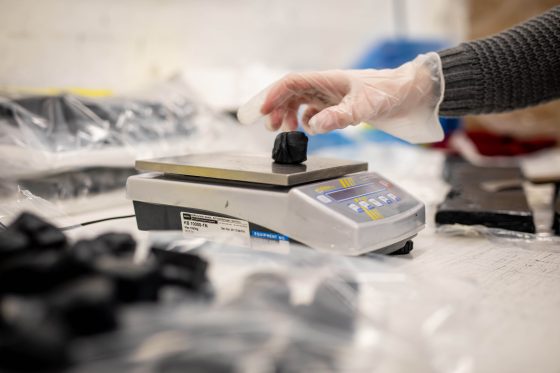
We’re sure it hasn’t escaped your notice that we’ve been around for rather a long time as a manufacturer. That means that we’ve seen some pretty extreme demand and supply challenges over the years (two world wars, three-day weeks, global pandemics, banking crises, fuel and energy shortages, extreme weather…). However, we cannot recall a time period with the combination of supply chain challenges that we’re currently seeing, nor the resulting levels of disruption.
Material supply issues are impacting our service levels and lead times to an extent that we can no longer absorb into our own processes. Therefore we intend to do three things: 1. Provide some clarity around where the delays are being caused, 2. Explain what we are doing to mitigate these challenges and 3. Explain what you can do to help us to help you.
What are the reasons for the supply issues?
- Sanctions on Russia
Oil and gas is a feedstock of many polymers, and carbon black is a critical component of many rubber compounds. Russia is responsible for roughly 30% of the world’s supply of both. This means that current sanctions placed on Russia have created a squeeze on these important raw materials – resulting in both material shortages and price hikes.
- Force majeure declared by 3M
3M are a key part of the global rubber supply chain and the recent forced closure of one of their European sites has resulted in a shortage of key ingredients used in FKM and FFKM (perfluoroelastomers). They have also terminated supply from one of their Russian plants, severing material availability from that source. 3M have, as a result of these events, declared a force majeure event.
- Competition with other markets
R142b gas is a critical component of FKM, and challenges in the scaling up of production (largely in China) combined with a huge increase in demand for the manufacture of lithium batteries for vehicle electrification has resulted in supply shortages and price increases.
Similarly, an increase in demand by the automotive and oil & gas industries has led to a deficit of the HNBR compound; key global producers do not intend to increase capacity but there is hope that the demand will abate in Q4 of this year.
- Energy crisis in China
China is in the midst of an energy crisis which has led to the introduction of rolling blackouts for their most energy-intensive industries. The majority of the world’s silicone feedstock comes from China, and with plants running at reduced capacity we are seeing shortages of all silicone compounds as a result.
- Impacts of Covid
Personnel absence as a result of Covid is still impacting staffing levels on many production lines and, as a result, some suppliers are choosing to consolidate production runs or stop specific lines. The impact further down the supply chain is in much longer lead times on some constituent ingredients. Added to this, the port of Shanghai is currently closed due to a city-wide lockdown, meaning that containers of already limited silicone supplies are unable to leave for export.
In all, there are 90 ingredients that go into the compounds we purchase which are currently all but impossible to get hold of by our own suppliers, regardless of the price that we or our customers are willing to pay.
What are we doing?
We are holding increased stocks of our most commonly used compounds. However, raw rubber materials have a limited lifespan (some last just weeks, others 6-12 months), which means that we have to be realistic about balancing material stocks against known demand.
Due to this limitation on shelf life we are actively creating forward order call-off schedules on our key suppliers for our materials in most regular use, to help our suppliers in turn better manage their own forecasts and production schedules.
We are also expanding our supply chain and qualifying new suppliers; however, we already have excellent relationships with our key, approved long-term compound suppliers and, given that this is a global supply shortage, a wider supply base is unlikely to have much of an impact on material availability.
What is likely to happen during the coming months?
Supply: Whilst the supply issues with some types of compound may ease as production opens up due to Covid impacts coming under control, in the vast majority of cases the supply chain issues have other origins and are likely to remain for at least the rest of this year. We cannot influence those shortages or provide any guarantee of when or where they will occur.
Pricing: The rubber compounding industry has seen some significant price rises over the past 12 months and those are likely to continue to increase – erratically in some cases – particularly where we are competing with other industries for ingredients, in combination with basic shortages.
What can you do?
Hold stock: Given that we cannot guarantee to hold prices, nor to supply within your usual expected timeframe, carrying a buffer stock of finished goods may provide you with a backup. Whilst raw rubber compound has a shelf life of weeks or months, vulcanised rubber will last at least 5-7 years, much longer in many cases. Please see our guide to the recommended storage conditions for cured rubber products.
Place a scheduled order: If you are unable to hold stock but can forecast with reasonable certainty, you could provide us with a bulk order to be delivered to schedule. This will allow us to purchase scheduled material in bulk now, to be manufactured for delivery as you need it and at the current cost base.
Allow longer lead-times: For materials where force majeure has been declared (FKM and FFKM materials), then all bets are off and we can only source materials as they become available. However, for other raw materials where the delays are due to temporary reduced availability, the best action you can take is to provide longer delivery windows for us. We would advise 10 weeks where possible.
Pre-warn your customers of delays: If you’re unable to take any of the actions above because you can only respond to demand as it arises, then we urge you to warn your customers of likely delays and look to them to respond to some of the calls to action above.
The current mix of complex social, economic and political challenges facing the global supply chain are unprecedented in our experience. The only thing we can currently be certain of is that there will be disruption to deliveries of our raw material – and therefore your finished product – over the next 12 months at least. Let us help you by working with you on the best route to success; speak with our service team so that we can find a solution that works for you and your customers’ needs.