How to test the quality of rubber
Posted on 09/08/2021 Category: Rubber Testing
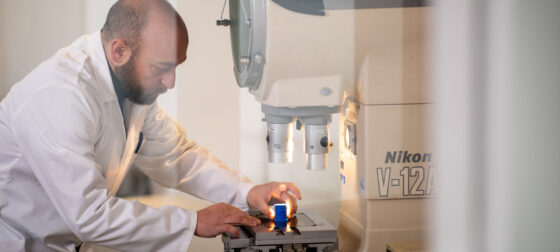
Have you ever had the o-ring on your garden hose split and leak everywhere? Annoying, isn’t it? If your first thought is that it’s due to a poor quality of rubber, think again. Many o-rings are made from NBR (nitrile) because most o-rings are used in applications to seal against oil, which NBR excels at. Unfortunately, it also degrades quickly in sunlight. It’s not a poor rubber quality issue, but it’s just the wrong rubber material for the hose application. We take a more detailed look at what we mean by rubber quality and how to test the quality of rubber.
What do we mean by rubber quality?
Before we look at how to test the quality of rubber, we need a clear understanding of the term ‘rubber quality’. Ensuring that you are working with the right quality of rubber might best be described as the process of ensuring that the product or material you choose is most suitable for the application you need it to perform. In other words, does it do the right job when it is brand new, and will it continue to perform at an acceptable level for as long as you want it to?
This analysis can be broken down into two areas: firstly, whether the mechanical design is correct, ensuring the product is functional and reliable, and secondly, whether the rubber type and grade are suitable for the conditions in which it will operate.
If the product’s design is sound and proven, which we can assess even before manufacture using non-linear finite element analysis, then we can begin to focus on whether the rubber quality is right for your product. To answer this question, we would need to know about the operating environment of the rubber part, as this affects the choices you should make in terms of the polymer type and the grade of that polymer to provide the performance and service life that you need within a specific budget.
One of the essential points to remember about ‘rubber quality’ is that it isn’t necessarily true that the highest grade, most expensive material available will be the best solution; instead, we recommend that you aim to use the most cost-effective and sustainable solution for the application, and it can often be the case that a lower cost, lower grade of material will perform perfectly well in meeting the design requirement and service life needed.
What is the difference between a commercial rubber and a specified grade of rubber?
Within the rubber family are many different polymer types, ranging from natural rubber that is tapped from rubber trees to synthetic rubbers derived from crude oil and other chemicals. They all have different strengths and weaknesses, and no single ‘magic rubber’ does everything optimally, so it is vital to understand the best polymer type for any given application.
Once the polymer type has been identified, the required operational parameters may dictate whether its performance needs to be formally defined as part of a specification. For example, if a particular level of chemical or temperature resistance is required or a tensile strength value must be met, this aspect of the ‘rubber quality’ will be designed to meet those targets, and if tested against those requirements, it becomes known as a ‘specification grade’. Such a rubber spec may be unique to a customer or meet an industry or international standard such as ISO, DIN, ASTM, etc.
Alternatively, the polymer choice’s general purpose—or commercial grade—may be suitable for the application. In this respect, properties such as chemical resistance, compression set, and tensile strength will be lower, but in many cases, will provide a suitable rubber quality for many products.
How do you know what quality of rubber is most suitable for your product/application?
Rubber technology is a wide-ranging topic with many subtle aspects; a slight change in the constituents in a rubber compound can dramatically affect the properties of the rubber products made from that grade, either to enhance or detract from performance.
General guidance on the typical strengths and weaknesses of the family of rubber types is readily available, but it is really important to fully understand the environment that a product will be working in; using the garden hose o-ring example, most o-rings on general sale are commercial grade NBR, rather than EPDM, which is the material best suited to the application due to its operating environment.
The level to which a rubber product is required to perform will then dictate whether a commercial grade of a rubber compound will be suitable or whether a higher grade of material, to a known and provable specification, is needed. That way, the rubber quality will be suited to your application and product needs.
How to test the quality of rubber
We are sometimes contacted by businesses receiving rubber components from other sources that are failing or underperforming where they were previously acceptable. This could be caused either by a change in the operating conditions or environment or by a reduced rubber quality due to a change in the rubber composition or the manufacturing process used for the part.
It can be challenging to perform rubber testing of quality on a range of finished parts or analyse why components begin to fail when historically they have performed well, but there are steps that you can take:
- Physical properties such as hardness and tensile strength can be checked if regulation size and shape samples can be created.
- Soak testing can be done to check fluid resistance.
- A TGA process can test the components to identify the chemical constituents destructively.
- Gas Chromatography can, if needed, provide further insights into the chemical constituents.
These laboratory tests on the quality of rubber are not routinely done unless a comprehensive failure mode analysis is required once a full review of the traceability with the supply chain has been done, along with a series of process checks and validations.
Unfortunately, it is all too easy within a global supply chain to provide documentation that does not reflect reality, and for safety-critical components, reliable, trustworthy suppliers and high-confidence processes are essential to ensure the product supplied is as it should be and continues to meet your specifications. Rubber moulding compound can be impacted when the supply chain has changed the composition to include higher proportions of lower-cost materials to ostensibly produce the same rubber quality.
Rubber tests we offer at Martins Rubber
- Hardness (Shore A and IRHD)
- Compression Set
- Load deflection
- Rheology (MDR)
- TGA
- Tensile stress-strain
- Peel
- Fluid Swell
- Vibration analysis
- Thermal Conductivity
- Radiation Resistance
Ensure Consistent Rubber Quality With Martins Rubber
To combat the issue of changes within compound make-up and to ensure that you have the confidence that there is adequate control over supply chains, choose a rubber manufacturer who only buys materials from credible, long-term suppliers and who can demonstrate robust quality systems and proven laboratory facilities to continuously monitor the adherence to the specification of the materials used.
Whether our rubber moulding compounds are specification or commercial grade, we only use highly competent and trustworthy suppliers based in Western Europe, where we have the confidence and track record to assure us that what we receive and process meets expectations. We have in-house testing of the cure profile of any material batch via our MDR, and we undertake hardness and compression set testing routinely to ensure that our finished products meet the rubber quality standard required of any given material or product.
If you are concerned about the quality of rubber for your future projects or would like to discuss how to test the quality of rubber parts you have had manufactured elsewhere, be sure to contact us, and our expert team will be able to guide and support you in finding the most suitable way forward.